Changes
made to Intelli-MAX Premium since version 32.0, Patch #7, which was
released on 2/5/2021
Changes
made to Intelli-MAX Premium since version 32.0, Patch #6, which was
released on 7/13/2020
Changes
made to Intelli-MAX Premium since version 32.0, Patch #5, which was
released on 1/17/2020
Changes
made to Intelli-MAX Premium since version 32.0, Patch #4, which was
released on 7/7/2019
Fixed
a bug in Make that
would cause the Card deceleration values for X and Y to be used when
jogging the rotary axis,
instead of the correct rotary axis deceleration valued.
Fixed
a bug that could cause some non-OMAX
.ORD files created by OMAX
competitors to import incorrectly, if the arc sweeps more than 180
degrees.
Fixed
a bug in the array
nester and percent utilization calculator where "areas" were
reported incorrectly if any unit other than Inches was active.
Fixed
a bug in the 3D Path
Editor where the "Assign Tilt" buttons incorrectly had the "Z
button" popup menu assigned to them.
Fixed
a bug in the 3D Path
Editor where if a mouse button were held down to zoom, and the
mouse wheel was then used while the mouse button was down, that the
editor may lock.
Fixed
a bug that could cause the "Join" command in the 3D Path Editor to sometimes flip an
arc around to the incorrect direction.
Removed
a "beep" that could occur in the 3D
Path Editor when pressing the
"Esc" key to cancel a command.
The
Gear Generator has
been
improved to allow for more combinations of gears to successfully
generate. In particular, it now handles many gears with higher
teeth
counts.
Fixed
a bug in Make that
could cause Rotary Axis velocities to be different than specified.
Fixed
a bug in Make that
could cause all rotation values in the "Locate
Part" dialog to be incorrect if the rotation angles needed for
correction are
large and the machine is configured for non-square motor steps.
Fixed
an obscure bug in Make that
could cause a "Range Check Error" when doing a "Vector Move" in the
event that the machine is configured to move at data rates faster than
the USB card can handle them.
Removed
the "Chrome" option in the Reference Geometry dialog of
the 3D Path Editor because it
is a frivolous feature that can cause an error message on some
computers / video cards.
Fixed
a bug in Layout that
could cause improper True Type Font scaling when importing files from
other CAD systems.
Fixed
a bug in Make that
could cause tilt in the incorrect direction if purposeful tilt is used
with the Tilt-A-Jet, and the total amount of tilt exceeds the
specifications of the Tilt-A-Jet.
Fixed
a bug in the 3D Path
Editor that
could cause an incorrect tilt direction if the "Mirror X" or "Mirror Y"
command was used on a path that contained purposeful tilt.
Fixed
a bug in Make
that
could cause an incorrect tilt direction if the "Flip" command in the
Change Path Setup was used on a path that contained purposeful
tilt. (Note: Using "Flip" on 3D paths is generally not
recommended because of the ambiguous definition as to what "Flip" may
mean in a 3D context. If you do use this command, do so with
caution, and carefully preview your part, dry run, etc., prior to
pressing "begin".)
Fixed
a bug in Make
that
could cause X/Y correction to be in the wrong direction when
non-standard stand-off values are used for A-Jet or Tilt-A-Jet equipped
machines.
Fixed
a bug in the "all variables" report
templates that could cause a
minor error message to display in Make when they are used.
Fixed
a bug that could cause the Tilt-A-Jet
to tilt in the wrong direction after a corner-pass when cutting a part
with tilt assigned to the entities neighboring the corner.
Fixed
a bug in Layout
where the "Zero" snap would cause the "Rotate Copy" command to exit
prematurely.
Fixed
a bug in Layout where
it was possible to create a tool path that would loop for infinity when
using slits.
Fixed
a cosmetic bug in the OMAX_SendMail.exe
application that could cause the bottom buttons to shift
after growing / shrinking the form.
Fixed
a bug in Layout that
could cause text to import as what would appear to be an "alien
language"
for a particular rare flavor of DXF file.
Fixed
a bug in Make that
could a Tilt-A-Jet to tilt in
the opposite direction desired when the Generation 3 cutting model was
used in conjunction with a thick part, and a specific small radius
inside corner.
Fixed
a bug that could cause 64
bit computers to automatically un-register the OMAX software in
some cases.
Fixed
the "7" and "8" characters in the MIK
Goudy font (prior to
fixing, the file for "7" was missing and the file for "8" generated a
"7")
Fixed
a bug in the "Import Settings" command in Make that would allow the settings
for OMAX Watcher to be inappropriately copied to the new computer.
Fixed
a bug in the "Inquire Motor Step" command in Make that would cause water-only
cuts and slits to be considered traverses.
Fixed
a bug in Make where
a water-only Quality attached to a lead could confuse the interpolator.
Fixed
a bug in Make's
Inquire Motor Step command that would cause the Newton speed to be
reported instead of the cutting speed when inquiring a water-only
section of the path.
Fixed
a bug in Make
that
could allow a jog command to stay active if the Windows Menu key was
accidentally pressed while doing a keyboard jog.
Fixed
a bug in Layout that
could cause extremely high radius arcs to convert to a series of line
segments when the "Auto-Path" command was used.
Fixed
a bug in the 3D Path Editor where the "Save" command
would
behave as a "Save As" if the file name or path of the presently open
file contained a period in it.
Fixed
a bug in the DWG/DXF importer that was possibly only in
previous Beta software, where font definitions would disappear during
the conversion process (resulting in situations where the "Arial" font
might be imported as "Times", for example.)
Fixed
a bug in the expression
evaluator where if a trig function evaluated to a negative
value, and the previous operator was a negative sign, then in some
cases the double negative would be incorrectly evaluated, corrupting
the ability to properly evaluate some expressions. The expression
evaluator is used anywhere a numeric entry is asked for throughout all
OMAX applications, though this bug would typically only be experienced
in the "Function Plot" command,
or when working with parametric OMX
files.
Fixed
a bug in Layout that
would cause the "Limit" snap to incorrectly snap to (0,0) if all
elements of the drawing are selected.
Fixed
a bug in Layout where
the "Perpendicular" snap was improperly enabled during the "copy"
command, resulting in a goofy display issue if the snap were used. (Now
it is properly disabled.)
Fixed
a bug in Make
that
would allow the stack height calculator to run
for water-only cutting paths, which would otherwise cause an infinite
calculation because water-only cutting does not use a cutting
model. Now, the stack height calculator button is properly
disabled for water-only paths.
Tilt-A-Jet
bug fix: A bug was found in Make
that could
cause very slight inaccuracies in tilt when the Tilt-A-Jet is used at
high
angles.
Fixed
a bug that could cause an exception error when importing
a
DXF or DWG file with a particular rare form of spline geometry in it.
Fixed
a bug in Make where
the hint shown in the edit boxes for the "Move to X/Y Coordinate"
command would always show units in Inches, even if an alternate
measurement system was active.
Fixed
a bug in Make where
external corners were sometimes using a slower corner model than
necessary, resulting in slower parts than necessary. This bug fix
will improve the cutting speed on external corners where corner passing
is not used, resulting in slightly faster parts.
Fixed
a bug in Make where
some "recompile with..." menu items would stay enabled when they should
have been grayed out if a bitstream file was open.
Fixed
a bug in Layout that
could cause an exception error under certain conditions when using the
"smooth" command.
Fixed
a bug in Layout that
could cause invisible layers in a DXF/DWG file to show up when they
should not.
Fixed
a bug in Make that
could cause a button on the Z numbers display panel to display the
wrong size in a rare situation.
Fixed
a bug in Layout that
would incorrectly report the location of the automatic backup file in
Vista and newer.
Fixed
a bug in Layout that
could cause an extra line to be drawn when using the SHIFT key to
constrain the Continuous Line Draw command.
Added
two 3 second delays into the automatic squaring routine
in Make used by the
Tilt-A-Jet to
ensure that each axis has adequate time to detect the hard stop has
been hit. This eliminates a very rare issue that could cause the
nozzle to be out of square.
Fixed
a bug in the "Rockbar Connect" font that
placed the tool offset to
the wrong side of the path for features of the capital "M" and "N"
characters.
Fixed
a bug in Layout and Make that
could cause unit switching to not be recognized in the Dutch and
Russian translations.
Fixed
a bug in
Make where
a change to any of the 3 drill delays would not cause the "ok" button
to enable or disable based on invalid data entered.
Version 14.0
Changes made
since rev "13.0" of the software, which was
released 2/27/2009.
Layout
New
command
"Resize Selected Arcs to New Radius": This allows one to
quickly
resize multiple holes at once without the holes loosing their
center points.
- Auto-Zoom on Re-size -
When
the Layout window is re-sized, a "zoom extents" now occurs.
- Updates to file filters
- Updated DXF / DWG filters for improved results on some rare
flavors of DXF/DWG
- Improved results importing some PDF files
- When importing PDF files into the white color scheme, the PDF
now imports slightly "whited out" in order to improve visibility of
vector lines drawn on top. (This adjustment can be overridden by
the user in the "Adjust Image Colors" dialog.)
- When importing certain common file formats (DXF, DWG, PDF,
SVG), it is now possible to use the "Esc" key to cancel the importing
(or preview).
- When importing files, hold down the "Shift" key when pressing
"Open" in the dialog to skip the preview / settings screen, and simply
use the last options chosen.
- Several new raster file
formats now supported for image tracing.
- Image tracing will now allow importing
of HUGE raster images. If an image is determined to be
huge (meaning that the current computer won't display it using standard
Windows image manipulating routines), then it is automatically shrunk
down to a lower resolution (where previously it would simply give
up). Note that quite large images can typically be loaded
without shrinking (depending on your hardware setup and such), so this
option is rarely invoked.
- 3rd party plug-in support: Added
support for an upcoming 3rd party plug-in.
- Added a "white level" adjuster
in the form for adjusting the
image for manual tracing. This allows images to be "whited out" a
little bit, making them nicer to work with when using the white color
scheme in Layout.
- Added more info reported
in the "Tech Support Report" feature.
- When using "Alt+Tab" to
switch between windows, Layout now reports the file that is in use,
making it easy to distinguish between multiple instances of Layout on
the same computer.
- The "Open Path in Make" menu
item in Layout now features an
auto-close Make option, in the event Make is already open.
- Improved performance of
routines throughout the software that use
rotations (rotate commands, nester, etc.) slightly, resulting in
marginal speed improvements in the nester, as well as functions such as
"rotate" that use these shared routines.
- The Create Report for
Technical
Support feature now allows entering of multiple email addresses
to "carbon copy" the report to when using the "email"
feature. It also reports a few new items useful to
technical support for diagnosis.
- Layout no longer redraws the screen multiple times when it is
first opened (a fix to a minor annoyance).
- Added compound keyboard combination for "Select Quality X", to
select a Quality. For example, press "S", then "Q", then "3" on the
keyboard to select all entities of Quality of 3. Also added
similar
option for "Deselect".
Make
- Added option to the "Advanced / Administrator Setup" dialog for
"Reverse Rotary Direction",
which can
be used in the event the rotary axis is physically flipped around on
the machine.
- Added 3 new materials
to
the database (A new form of Brass, Silver, and Niobium)
- The Generation 3 cutting model
has been improved slightly to allow better predictions when nonstandard
size mixing tubes are used. The following nozzle combinations are
supported with different degrees of testing. Other nozzle
combinations are also supported with less testing and lower accuracy:
Jewel
Size Mixing Tube Diameter
(inches)
(inches)
0.014
0.030
0.010 0.021
0.014 0.042
0.015 0.048
0.020 0.042
0.007 0.015
0.015 0.042
In addition, numerous tweaks and minor
adjustments have been made throughout to improve results based on
customer
feedback and additional testing.
Important
Note:
OMAX is always working to make the
Generation 3 cutting model predict and compensate for jet behaviors,
and create
parts to the specified cutting qualities as accurately as
possible. We do
this by continuously gathering data based on real world cutting, and
adding
this data into the model. Sometimes we discover that new data
causes the
cutting to occur faster than previous iterations of our models, and
sometimes
we discover that new data causes the cutting to occur slower. In
either case
this new and more accurate data is added to the model to allow the
model to be more
accurate.
When you upgrade to newer versions of the software, expect to see these
changes
reflected in the cutting times of your parts, and the edge Quality -
Your part
will more accurately be the edge Quality specified. If you find
that the
parts cut significantly slower than previously, you will find that the
parts
also are of better (and more accurate Quality of) surface finish.
If you
need to fine-tune the cutting speeds in order to match times of
previous
software versions, it is recommended you adjust the machineability
setting
slightly. For larger changes, pick a higher or lower cut
Quality.
Using the Generation 2 cutting model also an option, but is not recommended
due to it being less precise.
- Added more info reported in the "Tech
Support Report" feature.
Low pressure
"Locating Beam":
It is now possible with machines equipped with the "Pull to Open Valve"
to use a low pressure stream of water as a locating device, via a new
"Locating beam" feature. This feature requires an OMAX pump with
sufficient charge pressure, and a Pull to Open valve.
- Improved tool offsetting
routines slightly for better results
under some rare conditions, such as when working with tiny lead ins, or
at some specific line to arc transitions.
- Modified corner passing
slightly to be used slightly more often on arc corners.
- The Create Report for
Technical
Support
feature now allows entering of multiple email addresses to "carbon
copy" the report to when using the "email" feature. It also
reports a
few new items useful to technical support for diagnosis.
- Added 38 new variables to the
Custom Reports feature to to report statistics relating to what
"Quality" the part is made in. Of particular interest is
[OMAX_PredominantQuality] which reports the cutting Quality of the
largest length in the path, and [OMAX_PathQuality] which reports the
overall Quality of the entire path, or "Various" if the path is a mix
of qualities.
- Added a new report template
"Basic" which is a bare minimum report useful for quoting.
- Updated the "Z" toolbars to move with the Make window when the
Make window is moved.
- Bitstream Filter: OMAX’s
unique machine control is capable of controlling the motion of the jet
very precise with highest resolution. This gives the user a competitive
advantage especially at complex and intricate cutting geometries by
saving a significant amount of cutting time through smart machine
control. However, there may be rare cases where the high dynamics of
the cutting path can cause unexpected striations on the cutting edge.
To avoid this effect a “Bitstream Filter” can be applied. It is
disabled by default and can be enabled in the ‘MakePreferences.INI’ by
setting "WidthOfBitstreamFilterX" to a recommended value of 200 (value
0 disables the filter).
Introducing: Intelli-MAX Standard
- Intelli-MAX Standard is a special version of the Intelli-MAX
software branded specifically for the MAXIEM line of low-cost
waterjet machines. The Standard version of Intelli-MAX should
be familiar to any
OMAX user, but the Premium version for OMAX customers contains over 50
additional features (for example
corner passing, Intelli-PIERCE, Tilt-A-Jet support, and higher
resolution motion calculations).
- As an OMAX customer, there is no compelling reason to use
Intelli-MAX Standard, because the premium version that you already have
contains all the features in Standard, and more.
- MAXIEM machines can only run the Standard version of the
software,
and security measures are in place to prevent the Premium (OMAX)
software from running on a MAXIEM machine.
- OMAX Routed Data (.ORD) files generated with either the
Standard
or
Premium versions of the software will run on any OMAX or MAXIEM
machine.
- Note: Intelli-MAX Standard is not part of the standard OMAX
Software
setup program. It is mentioned here only for the awareness of
OMAX
customers.
Above: Maxiem Waterjet model
1530
running Intelli-MAX Standard (Click images for more info)
Installation
program
- No need to un-install first: The
installer now automatically updates on top of Version 13.0 or older
without bothering the user to un-install the old version first.
(Though when installing over Beta versions, it may still prompt you to
un-install first.)
- Faster install: Cleaned
up some code internal to the installer to reduce the overhead doing
multiple file copying, making the installation cleaner and faster.
- Reduced interaction: Only
one elevation prompt when installing for Windows Vista or Windows 7,
and fewer dialogs to deal with unnecessarily.
- Support for Windows 7:
Some minor changes have been made to ensure best support when running
on Windows 7.
OMAX
Interactive Reference
- New content has been
added, including:
- Drill and tap chart (with handy shortcut from the "Help" menu
in Layout)
- Expanded troubleshooting section
- Other new and updated content.
Bug
Fixes
- Fixed a bug in Make that
would cause multiple copies of a part to be printed, if previously the
user had chosen to print multiple copies of the statistics.
- Fixed an uninitialized variable that could surface as a bug in Make, but has not actually caused a
problem to our knowledge.
- Fixed a bug in Make that
would cause an "excess steps" error message to sometimes display for
insignificant amounts of error if units are set to millimeters.
- Fixed a bug in Make that
would cause Tilt-A-Jet equipped machines to tilt for the cut-off-saw if
a taper offset is entered.
- Fixed a bug in Layout that
would cause SVG files to be incorrectly imported (ignored) based on
settings used for previously importing a DXF or DWG file.
- Fixed a bug in Layout where
using the "X" button to close the "pick offset side" dialog would cause
the command to continue on as though the "ok" button were pressed
instead of canceling the command.
- Fixed a bug in Make that
would incorrectly print the "part history" when the user selected to
print the "notes".
- Fixed a bug in Layout that
could cause text and dimensioning to not import even when user
specified to do so for some DXF/DWG files.
- Removed link to "About" box in the Cooler Control application, to
prevent a potential lock-up that could otherwise occur.
- Fixed a bug in Make that
could cause calculations for "Tilt-Forward" to occur even if a
Tilt-A-Jet is not attached to the system or is disabled. This bug
was causing significant unnecessary slow downs for some parts on
non-Tilt-A-Jet equipped machines.
- Fixed a bug in the tool path interpolator in Make that could cause a lock-up in
the event "recompile pierces only" was done on a path that contained
only a single pierce point without any cutting, and the drill accessory
is enabled.
- Fixed a bug in the Tech
Support
Report generator that would cause two copies of the same report
to be sent in emails.
- Fixed a bug in Layout and
Make that
could cause a tool offset glitch in the case of very specific arc to
line geometry, where the resulting offset line would exactly intersect
a quadrant point of the original arc.
- Fixed a bug in Make that
would cause the last event triggered in the "test pump" form to run a
second time, after it had completed, if the user first starts a test
pump, then changes focus to another application, and then while the
focus is elsewhere the test completes, then the user right-clicks on
Windows Make in the task bar.
- Fixed a bug in Make that
cause the message "Stopped from baby-sit" to appear many times in a row
if baby-sit is triggered during a jog, and the source of the trigger is
not fixed.
- Fixed a bug in Make that
could cause corner pass lengths to be the incorrect length (too short),
resulting in "stuck corners".
- Fixed a glitch in the letter "D" of the Ekstrom Times Connect font.
- Fixed some typos in a few error messages in all applications
- Fixed a bug in Layout
where the "View existing path" option was enabled for drawings that had
no associated path.
- Fixed a bug in Layout that
could cause a beep noise when it first starts
- Removed some files from the installer
that would conflict with
Windows Embedded.
Rev
13.0
Changes made
since rev "12.0" of the software, which was
released 12/10/2008.
International
Languages
- New Russian and Dutch
translations. The official list of supported languages is
now:
- English
- German
- French
- Italian
- Spanish
- Polish
- Chinese
- Japanese
- Russian (new!)
- Dutch (new!)
- These alternate languages may be downloaded from the OMAX
Technical Support web site, or ordered on CD or DVD.
Layout
Updates to File
Importing
- Updated DXF / DWG filters for improved results on some rare
flavors of DXF/DWG
- Various bug fixes (See bug fix list below)
12
new
high-quality tool path fonts. New fonts are: MIK Aladin
stencil, MIK Aladin stick, MIK Brandy stencil, MIK Brandy stick,
MIKCentury Bold stencil, MIKCentury Bold stick, MIKcbkugein stencil,
MIKcbkugein stick, MIK Advert stencil, MIK Coney stencil, MIK Diner
stencil, and MIKAlgerian stencil.fnt.
- Small arc highlighting in tool
path: When previewing a completed tool path, areas of the path
where an inside radius is less than the specified tool offset are now
highlighted in Yellow because such areas can sometimes cause troubles
in tool offsetting. In most cases, such areas are automatically
fixed by the tool offsetter, but they are nevertheless
highlighted. Older DOS users must not ignore these highlights
because the DOS version of Make does not automatically fix such
areas. To force the highlights to appear, simply make a change to
the tool offset.
- Added error detection, recovery, and reporting in the event a
corrupt .ORD file was attempted to be loaded as part of a Tool Path
Font.
Make
- Additional
user lock-outs: Added options to lock out (password protect)
more features of Make. Specific items that are now password
protect able (in addition to what is already there): Zero Z home,
Go To Z Home, Zero User Home Button, Zero Active Home Button, Go To
User Home Button, Go To Active Home Button, Test Pump, Cut Off
Saw. These new lock-outs are not exposed in the user
interface. Contact techsupport@omax.com for details, if
you need to lock these features out. Other lock-out options are
on the Advanced / Administrator Setup screen.
- Cutting model tweaks to "Tilt
Forward" option:
- Optimized
some code to help prevent a small bowed cut-out that can occur when
cutting tight inside corners with the Tilt-A-Jet and "Tilt Forward"
enabled in thin materials.
- Slowed speed down slightly at cutting to lead-out transitions
when "Tilt Forward" is enabled to be still faster than without tilting
forward, but slower than in version 12. This prevents an issue
where under less than ideal cutting conditions the part might "stick"
to the scrap at this spot.
- Changed the default
value for the rotary axis
steps per revolution to 10,000 instead of 500,000 in order to reflect
the rotary axis hardware that OMAX actually sells.
Other
utilities and general changes
- The OMAX Interactive Reference
has been updated with new content and some minor changes.
- Jet Simulator utility
now
has a checkbox to enable an exaggerated version of the "tilt forward"
feature.
- Added additional file description encoded inside of "OMAX
Startup" so that its purpose is clear to system administrators who
might wonder what it is for. (OMAX Startup is a program that runs
briefly when Windows first boots. It sets a flag so that Make
knows whether or not the computer has been rebooted, which is used to
determine whether or not to nag the user to re-home the machine or
Tilt-A-Jet accessory. It is also used to launch the OMAX Cooler
Control application.)
- All applications now report their "build numbers" in the about
box.
Bug
Fixes
- Fixed a bug in Make that
could cause blemishes at corners with tiny entities if "tilt forward"
is enabled.
- Fixed two bugs in Layout
that could cause some files (Adobe Illustrator and PDF files,
primarily) to not import properly in the event the computer is
configured to use commas as the decimal character.
- Fixed a bug in Make that
could cause and exception error on paths that end with a very tiny
section of Heads Up Traverse.
- Fixed a bug in Make
that
could prevent the "key up" event to halt the "Jog" command in the event
that the jogging was being done with the keyboard, while the operator
simultaneously attempted to access right-click menus.
- Fixed a bug that could cause OMAX
Camera to have an exception error on the very first time it is
run after a new install
- Fixed a bug that could cause display corruption of the "There
are
updates available" button in the About
Box when running on some
non-English installations.
- Fixed a bug in Layout
that could cause an exception error and prevent the
"File / Import From Other CAD" option from working properly on Windows
2000 computers (Note that this bug was also fixed for version
12, but
required downloading of a "patch" to fix.)
- Fixed a bug in Layout that
could cause PDF files that do not contain any
vector data to not import anything at all.
- Fixed a bug in Layout that
could cause an exception error when importing
PDF files
- Fixed a bug in Layout that
could cause an error when using "Import from other CAD", if the file
being imported contained Unicode characters, and the "Import text" or
"import dimensioning" options were enabled.
- Fixed a bug in OMAX Camera that
could cause a silent "range check
error" when in the "Change Camera Resolution" dialog.
- Fixed the semicolon character in the "Stick" Tool Path Font to
work correctly.
Rev
12.0
Changes made
since rev "11.0" of the software, which was
released 7/2/2007.
Layout
Layout is now password protected using the
same password as Make.
This is to ensure the competitive
advantages offered by OMAX Layout are taken advantage of only by OMAX
customers by preventing non-customers from using Layout to program
non-OMAX
machines. If a valid password is not entered, then all saving,
and copy to clipboard operations in Layout will be disabled.
New and
improved file filters:
New ability to
DIRECTLY import Adobe
Illustrator *.AI files. Adobe
Illustrator is a very popular vector based illustration software
package used for heavily for artistic purposes. OMAX Layout will now
allow directly opening native Adobe Illustrator files by simply
choosing "File / Import from other CAD". Curves from Adobe
Illustrator are then smoothly converted to arcs in OMAX Layout -
eliminating messy issues relating to Adobe DXF file transfers, or the
need for third party translation utilities. Adobe Illustrator
*.AI files are now a preferred method for bringing in data into OMAX
Layout.
- Tip: It is strongly
recommended when importing files from Adobe
Illustrator to use Adobe
Illustrator (AI) files. Do not use DXF files. Although DXF
files are a generally recommended solution for nearly all CAD files to
be used on the OMAX, DXF files from
Adobe Illustrator are very messy and awkward to use.
- Tip: Maximum
support
is provided for Adobe Illustrator files version "CS" or
older. Adobe Illustrator CS2 and CS3 files are only partly
supported and may not import correctly.
Corel Draw CMX and Encapsulated Post Script
(EPS) Support: It is now possible to import most EPS files and a
few simple PS (Post Script) files, as well as most Corel Draw CMX files..
- Tip: When working
with Corel Draw,
use SVG files or CMX files, as the DXF files from Corel Draw tend to be
quite messy.
New ability to import vector data from
"SVG" file formats: SVG
files are "Scalable Vector Graphics" files that are typically output by
a wide variety of vector based illustration tools such as Adobe
Illustrator, and many others
typically used in
artistic applications. For more information on SVG files, see: http://www.w3.org/Graphics/SVG
Updated
DXF and DWG file filters: The latest filters support:
- New support for up to
AutoCAD version 2009
- Improved
AutoCAD 2007 importing
- Improved support for importing text from Adobe Illustrator
DXF / DWG
files (Though it is recommended to use AI or SVG files when working
with Adobe files)
- If a DXF or DWG file has more than one layout in it, then
the
"Layouts" combobox will slowly blink, drawing attention to itself.
- The slider for "Spline conversion tolerance" now allows for
a
wider range of tolerance values.
- Improved spline conversions to give better results on some
rare files
- Updated filters to support yet more "flavors" of DXF / DWG
Updated PDF file filters: PDF file
filters now "decompose" text objects into lines and arcs.
- The file extension "*.cnc"
is
now recognized as a valid file format for reverse posting g-code
files (though not all "flavors" of .cnc files are supported).
- Tip: For a complete
list of
file formats supported by the OMAX Software, and notes on each, type
"File formats supported" into the index of the OMAX Interactive
Reference.
Measure in "Pixels": If
there is an image showing in the background of Layout for Image
Tracing, then the "Measure" command will show the length of measurement
in the title bar of the results window in units of
"Pixels". This is handy for calculating "Pixels / inch" of
a photograph that has a feature of a known dimension in it - useful to
know when reverse engineering photographed parts, lining up tool paths
with the grains of marble, etc.
- Render as Solid
- Improved the resolution
of the "Render as Solid"
command, allowing it to catch finer details (though at a slight expense
in calculation speed, and memory used.) Tip: Hold down the "Shift" key when
clicking on "Render as Solid" for a quick render (at low resolution),
or right-click for an options menu.
- The right-click option to save to file now saves a file that
is
the same size as the rendering window (So stretch the window to the
size you want prior to rendering.)
-
Calculate
Percent Utilization:
A button for this has been added next to the "Render as Solid" button
in both Layout and Make to calculate what portion of a material is
utilized by the part.
- Improved Tool Offsetting: A
few "pre-filters" have been added to the tool offsetting routines to
remove some common geometry problems that otherwise cause tool offset
errors. In particular, tiny arcs in inside corners are now
tolerated a little bit better, as are tiny round holes. It is
still advised to avoid tiny arcs (or tiny entities in general) at
inside corners, but if you forget,
chances are it will now offset fine anyway.
- Added "Shift+B" for "Bolt
Circle" keyboard equivalent. Also added "Generate Standard
Shape" to the list of commands that hot-keys can be assigned to (which
runs the bolt circle command.)
18
new
high-quality tool path fonts: Seventeen of these fonts came
from an OMAX customer.
Note
that you can make your own tool path fonts, and if they
are of high-quality then OMAX would like to consider purchasing them
from you to then include in
future software updates. If this is of interest to you, be sure
to read the topics "Creating your own fonts for Layout", and "Checklist
for submitting fonts to OMAX" in the OMAX Interactive Reference.
- Added new sample files folder "Machine_Layouts"
which includes 1:1 scale DXF drawings of most OMAX machines and large
accessories. These can then be used for floor planning purposes
when planning to install or move OMAX machines. Tip: Use the
"Select Quality =" command to easily move just the portions of the
drawing you need.
- Add
spaces between characters in a tool path font: A right-click
menu item has been added to the "ABCD" button in the Tool Path Text
dialog to automatically add spaces between the characters. This
makes it quick and easy to build a DXF file of all the letters in a
tool path font, which is useful should you wish to edit the tool path
font, or use it as a starting point for a new font. Simply click
on the "ABCD" button, then right click on it to add the spaces.
Added
"permanent" shortcuts to common locations for storing OMAX files the
shortcut popup menu in the File/Open dialog.
Right-click on the folder list to
access these. Note that the "Public" and "downloads" folder
shortcuts
only show up if these folders are defined (typically in Windows Vista)
Make
New Generation 3 Cutting Model: The
three generations are defined as follows:
- Generation 1 – The
cutting model used in early versions of the OMAX software for DOS. This
cutting model was based on Dr. Jay Zeng’s doctoral thesis at the
University of Rhode Island.
- Generation 2 – A
modification of the above, with significant enhancements to support a
wider range of pump, nozzle, and material combinations, as well as
extended to support significant process improvements including improved
corner control, corner
passing, taper prediction and compensation, and fast piercing. This
cutting model was
introduced with revision “T” of the OMAX software released 1/21/2002
- Generation 3 – A
completely new model created from scratch with significant
improvements, as outlined below.
Some
key features of the new Generation 3 Cutting Model
include:
- Precision coverage of a wider range of thickness and types
of materials
- Precision coverage of a wider range of pump and nozzle
combinations (in particular it improves support for the OMAX “stone”
nozzles, high power pump and nozzle combinations, and any further
additions of the OMAX
nozzle family.)
- Improved prediction of taper, jet lag, kerf growth, and
other jet behaviors
- Support for separate modeling for different categories of
materials (So
“stone” can be treated differently than “metal”, etc.), which allows
for
greater precision in modeling the process.
- Much improved ability to expand and refine as more testing
is done in the future (This is a model that easily and quickly adapts
to new applications and new process capabilities.)
- Machineabilities for more materials now included with the
software
- For Tilt-A-Jet equipped machines:
- The jet now "tilts forward" in the cutting direction to
improve speed and precision at corners and arcs, as well as improving
edge finish (or cutting speed) along straight sections.
- Improvements have been made in arc-to-arc and arc-to-line
transitions, reducing “boogers” at such points in thick materials.
- Improvements have been made to eliminate "kick back" from
ricocheting after corner passing in thick materials.
- Because of the above and other changes, Tilt-A-Jet users
will see significant improvements in cutting speeds for most parts.
- The old cutting model (Generation 2) can still be used via
a
setting in the Advanced / Administrator Setup dialog. The version 2
model has also been updated with minor changes to include better
support for additional nozzle combinations, but otherwise stays the
same. In particular, the older model has been updated to improve
results with 0.015/0.048" and 0.014/0.042" jewel / mixing tube
combinations.
- Additional configurations for the advanced user are exposed
in the "Cutting Model" tab of the Advanced / Administrator Setup
dialog. Some of these configuration settings work for both
Generation 2 and 3, and some are unique to 3.
In order to take advantage of the
Generation 3 cutting models, there have been some significant changes
to the user interface of OMAX Make:
- The materials database has been re-worked to organize the
materials it contains into different “categories”. This allows the
cutting model to treat each category of material differently and be
significantly more precise. This precision then translates into better
speed for some materials, and better precision for others. Because the
cutting model now needs to know this category, the user interface has
changed to ask for it.
- It is now much easier to add and remove materials from the
database, and there is no risk of adding a material to the database,
and having OMAX overwrite it in the future. It is also much easier to
share custom materials with other OMAX users or machines. This is
because instead
of a single file that contains all the materials that is difficult to
edit and expand, each material is now stored in its own file that is
easy to copy and share.
- To copy custom materials to another computer, simply copy
the material files into the appropriate folder. OMAX materials are
stored in a different folder than user materials, so there is no risk
at all of OMAX materials overwriting or erasing user materials when the
software is updated later on. To easily browse to the Materials
Folder using Windows, simply choose "Explore Materials Folder" from the
materials menu in Make. Be sure to copy all "user" materials to
and from the "user" folder.
- “Legacy” custom materials from prior to release
12.0 of the OMAX software are automatically transferred
over to the new system, and categorized in the material category
“legacy”. Note that these materials are missing important information
about what “category” they belong in; therefore, the OMAX has to make
safe assumptions about these materials, and not all benefits of the new
cutting model will be utilized when selecting materials from this list.
However, it is easy (and recommended) to edit these materials and move
them into specific categories for better performance – especially in
future software versions.
- Because the material list can become quite long, it is
possible to hide infrequently used categories of materials. For
example, if one does mostly metal work, and rarely stone work, it is
possible to easily hide stone materials from displaying in the list.
They can be re-displayed later when needed.
- An additional check-box has been added to the "Cutting
Model
Setup" dialog to enable or disable the Tilt-Forward feature. (See
important note below on why one might wish to do this.)
Important
note to Tilt-A-Jet users:
The Generation 3 cutting models provide a tremendous speed increase for
many parts, due to the introduction of the "tilt forward"
feature. Unfortunately, this feature requires precision
calibration of the Tilt-A-Jet hardware - beyond the precision as
may have been previously shipped from the factory for older
Tilt-A-Jets. If the Tilt-A-Jet is not
precisely calibrated, it is likely that the "tilt forward" feature will
result in inaccurate parts due to X/Y shifting at the extreme tilt
angles used in many
cases. Because of this possibility, the "Tilt
Forward" feature is disabled by default when upgrading the software.
This feature can be easily enabled from
within the
"Cutting Model Setup" dialog (the same dialog where corner passing and
such can be enabled / disabled.) OMAX will be
offering a precision calibration service as well as the option to
purchase the necessary equipment for those who prefer to do this
service themselves. Contact OMAX
Technical support (techsupport@omax.com) for details.
- Q: I went to manually enter in a machineability for a
material, but the machineability edit box was grayed out and it would
not let me. Why is this, and what do I do?
- A: The new cutting model needs to know what “category’
of material this machineability is to be classified under. Choose the
option in blue text in the appropriate
category for your material, and it will then allow you to manually
enter in a machineability.
- Q: I notice when compiling tool
paths that there is a slight pause at the start of compiling when using
the Generation 3 models, what's with that?
- A: The Generation 3 cutting
model recalculates some data at the start of compiling. This takes a
fixed amount of time, regardless of the tool path.
- Q: I notice that “Separation
Speed” is now reported. How is that different than “Quality of 1”?
- A: Separation speed is the
speed required to separate the material under ideal conditions (perfect
nozzle, etc.) Quality of 1 is slowed down to ensure part separation in
slightly less than ideal situations.
- Q: Can I use the older
Generation
2
cutting models if I want to?
- A: Yes. It is possible to
choose between “Generation 3” and “Generation 2” cutting models in
the “Advanced / Administrator” setup. Note that the Generation 3
cutting models are typically more accurate than the Generation 2
cutting models, especially for nozzle combinations other than 14/30
(Standard Maxjet4 and Maxjet5) and 10/21 (Minijet).
- Q: What kind of speed-up (or
slow down) can I expect when using the Generation 3 cutting model,
when compared with the Generation 2 model?
- A: Since the new cutting model
allows for better prediction of tool behaviors, in general parts will
cut quicker, but this is not true for all parts. Actual part cycle
times will vary slightly when compared to the same part cut with the
Generation 2 cutting model. Some parts may be slightly slower, and
some parts may be faster, however for all parts, the cutting model will
more accurately produce the part to the desired “Quality”. For thick
parts with many inside corners and small arcs, a speed-up
is likely. Tilt-A-Jet users will also see significant speed up
improvements for corners and straight line cutting, due to the new
"tilt forward" feature. Compiling of the tool path will take
slightly longer due to
a few seconds required to initialize the cutting model.
- Q: What kind of change in part
precision can I expect when using the Generation 3 cutting model,
when compared with the Generation 2 model?
- A: For those following
precision practices, part precision will typically be better,
especially at arc-arc or arc-line transition points. Surface quality
may appear to be “upgraded” slightly in some cases. However, for most
users, the
precision may not be noticeably different, except in cases where the
Generation 2 model was significantly lacking, for example, when nozzle
combinations other than 14/30 and 10/21 are used.
- Q: What is the range of
parameters that the Generation 3 cutting model can handle, and how
does that compare with Generation 2?
- A: Compared with Generation 2,
the boundaries of parameters that the Generation 3 cutting model
can handle are always on the move (expanding). Currently it supports
the OMAX standard nozzles (14/30 and 10/21) mostly reliably and the
newly released nozzles (14/42, 15/48, 20/42) moderately. The current
ranges of the other parameters are: pressure 20 – 60 KSI, material
thickness 0-6 inches, abrasive mesh 50-220 (limited by nozzle size),
and abrasive flow rate 0.1-3 lb/min (limited by nozzle size). Using the
model outside these current ranges may generate less than ideal
predictions, similar to the Generation 2 model. However
feedback of new applications and demands from the users will drive the
expansion of these boundaries continuously.
- Q: Now that I am using the new
system, I would like to copy all the custom materials I have made from
my OMAX machine to my office PC. What do I copy?
- A: Each material is saved as
its own file in the ..\Materials\User\ folder. Simply copy the
materials from this location on your OMAX machine to the same location
on your office PC. The next time you run OMAX Make, the materials will
be automatically detected and added to the list you can choose from.
Note that the “Materials” folder is typically in your C:\Program
Files\OMAX Corporation\OMAX_Layout_and_Make\Materials\ on Windows 2000
and Windows XP. However, the location is in the
C:\Users\Public\OMAX_Corporation\AllUserData\Materials\ Folder under
Windows Vista. To easily browse to the Materials Folder
using Windows, simply choose
"Explore Materials Folder" from the materials menu in Make. Be
sure to
copy all "user" materials to and from the "..materials\user" folder,
and do not use the "..materials\OMAX" folder (The "..materials\OMAX"
folder is used by Make exclusively, and is frequently erased and
re-created.)
- Q: I installed the software on my Tilt-A-Jet equipped
machine, and seem to be getting pretty good precision on my
parts. Should I still perform the precision calibration?
- A: If the part precision is perfectly acceptable to
you,
then there is no need for additional calibration. However,
additional calibration may be useful, especially if you do precision
work that is beyond the advertised specifications for the
machine. Calibration may be the difference between "good parts"
and "great parts", though there is some risk of performing the service
on an already perfect Tilt-A-Jet.
Rotary axis support: Basic support
for jogging and indexing a rotary axis is now part of the
software. Contact OMAX for information on hardware availability.
- Improved results in thin
materials with Tilt-A-Jet equipped machines: Some improvements
have been made to improve the results of thin material cutting with the
Tilt-A-Jet.
- Corner passing is now disabled
for features that exceed 60 inches/minute when the Tilt-A-Jet
is enabled. This prevents unnecessary slow-down and
vibration for many parts - especially when cutting thin or soft
materials.
- Improved machineability chart:
The machineability chart is now better looking, and provides the option
to show pierceability values in the same chart.
- Faster collision checking: Some
changes were made to speed up line to line collision checking, which in
turn speeds up calculation of corner passing and lead optimizations,
nesting, and other areas of the software that do collision checking.
- Optimized the lead in
calculations to take less time when
auto-growing lead ins for the fastest pierce. This improves
calculation performance slightly when working with huge tool paths with
many pierces.
- Specify material for paths
with
no cutting: It is now possible to specify the material and
thickness for tool paths that do not contain any cutting entities, but
do contain leads. This is useful when making paths that are
purely pierce points - for example fine hole drilling.
- Improved corner passing:
Some tolerances were adjusted to allow for corner passing on some
corners that previously would not, resulting in a small speed-up for
some parts.
- Improvements to "Homing"
- Machine homes are now saved
at
the moment the "begin" button is
pressed, to ensure that the Path Start Home is preserved in the
event
of a power failure during the cutting process.
- History files now record
"auto-home" events. This helps diagnose home related
problems related to users not homing their machines after machine power
downs.
- A 2 second delay has been added to the homing process after a
baby-sit is triggered, to prevent users who "cheat" the homing process
by pressing "pause" from accidentally causing portions of the homing
process to be skipped, resulting in homes being lost by a tiny
amount. Now, the homes will only be (potentially) inaccurate if
the button is held
down for longer than 2 seconds.
- Improvements to Tilt-A-Jet
Squaring:
- Make will now ask to
auto-square
the Tilt-A-Jet after the operator disables the Tilt-A-Jet in the
"Change Path Setup" dialog, in the event that the nozzle might
have been left in a tilted condition previously. This helps
prevent the possibility of cutting a part with the Tilt-A-Jet, stopping
it in the middle, with the head tilted, turning off the Tilt-A-Jet,
then cutting a new part with it left tilted by mistake.
- Tilt-A-Jet squaring is now a LOT
faster
- Soft limits: On
machines
that "home" in the +X or +Y directions (or both), it is now allowed to
enter in a negative distance when setting up soft limits by corner and
size. (Making it more convenient to set the soft limits
immediately after homing on machines such as the Fabricator, which home
in the +X direction.). Note that setting the soft limits
after homing is typically unnecessary, as the homing process itself
automatically restores soft limits. The only reason to reset the
soft limits after homing are: 1 - if the soft limits were corrupted by
setting them when machine had no established home position, 2 - if the
soft limits had never been set before, or 3 - if the location of the
absolute home is being moved elsewhere for some reason.
- Improved response to user when
"jogging" and "Bumping" slightly.
- Statistics display now shows
"Separation Speed", which is the fastest speed cutting that is
possible to still separate the material. This speed is
significantly faster than even a Quality of 1 speed, but carries the
very likely risk of not cutting all of the way through. (Which is
why Quality of 1 is purposely slowed down, and why "separation speed"
is not actually used for cutting purposes.)
- The Statistics box will now scroll in response to the mouse
wheel.
- Moved the setting for "Stall
Distance" from the "Motion Preference" dialog to the "Advanced /
Administrator Setup" dialog, because this setting is rarely changed,
and is confusing to users.
- "Advanced / Administrator
Setup"
dialog changes:
- Added option for an administrator to password protect OMAX Make from
running at all (in addition to the other individual password protection
options.)
- Rearranged some of the "Advanced / Administrator Setup"
dialog
menus.
- Added option to change the
number of significant digits
displayed in
the coordinate display ("Green Numbers"). Note that this will
allow setting more digits than will fit in the display, so it is up to
the user to be reasonable with this.
- Added a check-box that enables a button in the "Change Path
Setup" dialog that allows direct
access to the "OMAX Machine Setup"
dialog (so users can change pump and nozzle setup, timing, etc., from
within the "Change Path Setup" dialog.)
- Added new settings relating
to the Generation 3 Cutting Model.
- Added adjuster sliders to fine-tune
the deceleration of the Z axis while jogging to the "Speed
Limits & Homing" page. These sliders affect how hard the Z
axis comes to a stop when jogging using the mouse or keyboard.
- Improved Bitstream "BTS file"
loading, saving, running, and
previewing: (Advanced hidden feature) Many changes have been
made to
make it easier for
advanced users to use BTS files for advanced applications. BTS files
allow total control of the
motion and outputs of the machine at an extremely fine spatial and
temporal resolution, but at the same time are often quite difficult to
create outside of Make. Typically they are created for you
automatically when a
tool path file is "compiled" in Make, but they can also be made by
other means. Bitstream files for the current tool path are also
included as part of Technical Support
Reports, for shorter paths. New bitstream support includes:
- When BTS files are loaded statistics are
displayed about the path
- The "color preview" function now properly
displays colors as a function of speed.
- The "Zoom
Extents" command now properly zooms to the extents of the motion.
- The "Inquire Motor Step" command also now works on BTS files.
- If an error is detected in a BTS file during loading, then
the
Frame Number and approximate line number of the error are shown in the
error message.
- If an existing tool path is already in memory (whether loaded
from a previous BTS file, or a compiled tool path), then there is an
option to append the new BTS file to the end of the currently loaded
BTS file. This is a handy feature for "stitching" two BTS files
into a single file, and the resulting bitstream can be re-saved out as
a new BTS file, if desired. (allowing the creation of fairly complex
custom paths.)
- It is now possible to auto-start Make with a bitstream file
for
the purpose of automatic reporting
- It is now possible to auto-start Make with a bitstream file
for
the purpose of automatically running the machine.
- Saving of BTS files has been added as a right-click option to
some motion commands.
- Bitstream files now properly resume the jet state when
resuming
after being paused.
- Bitstream files now properly handle accelerations when
resuming
after being paused
- BTS file support is a feature that is normally hidden from
the
user. For more information on the BTS file and what it can
do for you, contact techsupport@omax.com.
Improvements to the Transfer
Settings feature:
The Transfer Settings command has been moved from the "Setup /
Advanced" menu back one level to the base of the "setup" menu, and has
been renamed to "Transfer / Backup Settings" to indicate that it is
also useful for backing up critical settings. In addition, it is
now
possible to save the settings as a .zip file with a name and location
of your choosing. One result of these changes is it
is now very easy to run quotes on an off-line computer for several
different OMAX machines configured with different configurations (Simply "import" the setup from
the machine you need to quote from.)
- Registration password
information is no longer
stored in "MakePreferences.ini". This
makes it easier to copy
MakePreferences
from one computer to another without "un-registering" the software by
mistake. This is useful, for example, in the case where job
quoting
for several differently configured OMAX machines is done on an office
PC. Simply copy over the MakePreferences.ini for the machine to
quote
for, and then run OMAX Make. (A simple .BAT file can be created
to
automate this process, if desired - or, of course, simply use the above
mentioned
"Transfer Settings" option in Make.)
Improvements to "Custom Reports":
- Many new variables have been
added For example, variables
have been added to expose the linear feed rates for the various
Qualities, calculated water flow rate, calculated horsepower at the
nozzle, separation speed, material category, and more. See either
the "All_Variables_Spreadsheet.xml"
or the
"All_Variables.rtf" OMAX
Template file for a list of all the existing
and new variables.
- Added a new OMAX Report
Template for "Linear Feed Rate Report", which produces a
document similar to the report generated by the OMAX Abrasivejet Feed
Rate Calculator. (Note that the OMAX Abrasivejet Feed Rate
Calculator" has been discontinued.)
- Custom Reports can now be
automatically generated via 3rd party applications.
For example, one can write software to launch Make, compile a tool
path, generate a report, and then exit. This is useful for
automated software testing, batch processing of OMAX files for quoting
purposes, and other automation tasks. Note that a special
password is needed in order to enable this feature. (email
techsupport@omax.com for details on interfacing.)
- Added ability for custom reports to take a screen-shot when
running in automated mode.
- Custom reports can now grab
data directly from INI files using the syntax
[OMAX_ReadINI_"IniFileName.ini"_Section_Identifier], where
"IniFileName.ini" is the name of the INI file to read from (for
example, "MakePreferences.INI"), "Section", and "Identifier" indicate
the section and variable name to read. This is useful to
read just about any setting one might need for a custom report that is
not otherwise exposed specifically.
- Some errors (errors in interpolation) are now exposed to
custom
reports. (Used mostly for in-house automated testing.)
- A progress bar now entertains the user while larger reports
are
generated.
- Improvements have been made to speed up report generation -
in
some cases very significantly
- Inquire Motor Step command now
displays the time from the start
of the path, to the point inquired. This can be used, for
example, to determine the time between two arbitrary points in the tool
path.
- Render as Solid
- Greatly improved the resolution of the "Render as Solid"
command, allowing it to catch finer details (though at a slight expense
in calculation speed, and memory used.) Tip: Hold down the "Shift" key when
clicking on "Render as Solid" for a quick render (at lower resolution.)
- The right-click option to save to file now saves a file that
is
the same size as the rendering window (So stretch the window to the
size you want prior to rendering.)
- Calculate Percent Utilization:
A button for this has been added next to the "Render as Solid" button
in both Layout and Make.
- Comments in OMX and BTS files
are designated by the "//" characters. In previous
versions of the OMAX software, these two characters would have to be at
the start of a line in the file. Now, they can also occur at the
end of a line in the file, to add comments to the right of whatever
data is on the line.
- Improved inter-process
communication to 3rd party applications: OMAX Make "broadcasts"
it's status via Windows Messaging to any applications that care to
listen. This might be used, for example, for machine tool
monitoring or control purposes via custom software (or MTConnect, etc). New to
this
release are some improvements in the efficiency of this process, as
well as some new configuration options, and a whole bunch of new data
that gets sent. Contact techsupport@omax.com for details.
- Improved Tool Offsetting: A
few
"pre-filters" have been added to the tool offsetting routines to remove
some common geometries that otherwise cause tool offset
errors. In
particular, tiny arcs in inside corners are now tolerated a little bit
better, as are tiny round holes. It is still advised to avoid
tiny
arcs at inside corners, but if you forget, chances are it will offset
fine anyway. It is also now allowed to enter in Tool Offset
values that are smaller than the smallest inside corner radius.
If such an offset is entered, the offset edit box will turn yellow as a
warning (as it always had), but the "ok" button will be enabled
allowing the user to compile anyway. As always, preview the tool
path carefully before pressing "begin", but be especially vigilant when
compiling paths where the offset edit box is yellow, since not all
possible errors are detected or corrected.
- Removed ability to specify
material to cut with the "cut off
saw". Cut off saw now simply uses whatever material is
currently
loaded for the current part. (This functionality has been removed
with the introduction of the Generation 3 cutting models, but will
may be
restored in a future software version, depending on customer feedback.)
- Removed a minor annoyance to
Tilt-A-Jet users: Make no longer asks the user to square the
Tilt-A-Jet prior to running the cut-off-saw feature, if the head is
already square.
- Added warning if total tilt
angle commanded to the Tilt-A-Jet is outside of limits: If the
combined tilting of taper offset, purposefully programmed in tilt, and
forward tilting for a path exceeds the maximum tilt angle allowed by
the Tilt-A-Jet hardware for at least one spot in this path, then a
warning is displayed to the user.
- Improvement to lead outs when
the Tilt-A-Jet is enabled: The interpolator and tool offsetter
now turn off the jet sooner at lead outs in order to save time on thick
parts, and reduce blemishes caused by tilting or dwelling at lead out
locations.
Specify plumbing resistance for high
pressure tubing: Advanced users can now specify whether
the pressure entered into Make is measured at the nozzle, or at the
pump (or some other location in the plumbing system). If
measured at the pump, then an option for a "Resistance Factor" can be
entered in, so that Make knows how to properly calculate the pressure
loss between the pump and nozzle, regardless of the kind of nozzle
attached. By using "Resistance Factor", it is possible to
accurately tell Make the exact pressure at the nozzle, even when
measuring the pressure at the pump with long tubing that causes
pressure drop. Using a "Resistance Factor" instead of a simple
pressure offset, enables this feature to automatically work regardless
of the
orifice size of the nozzle. This is set in the "Advanced /
Administrator Setup", and information on how to calculate or measure
the resistance factor is provided in the help screens. This
feature is most important for those with larger machines with long high
pressure tubing where pressure loss can be significant. Consult
the OMAX Interactive Reference for suggested values for various machine
configurations.
- Added support for a new
machine
types "80-X". This is a new large size OMAX machine using
traction drive technology, and can be extended to custom lengths in 2
meter increments.
Added "permanent" shortcuts to common
locations for storing OMAX files the shortcut popup menu in the Change
Path Setup dialog. Right-click on the folder list to
access these. Note that the "Public" and "downloads" folder
shortcuts only show up if these folders are defined (typically in
Windows Vista)
- Added code to prevent
accidentally loading non-tool path files into Make by using
"Open With" in Explorer, or similar. (In other words, if a file
type of either OMX, ORD, or BTS is passed to Make, it will open, but
other file types will generate an error message. Previously,
other file types would open, but open as a useless mess.)
- Power management features (hibernate,
sleep, etc.) are now disabled whenever Make is running, if Make is
configured as an actual machine tool. This prevents power
management features from stopping USB communication to the motors, and
eliminates the need to custom configure each computer to disable power
management functionality.
- New Diagnostic Tools
(typically used by OMAX Technical Support and Development):
- Added features to detect
delays
on the USB line (which can be an indicator of a noisy signal)
and log them the error log history
file. Line is checked for delays only at certain events, such as
the start of a jog or tool path. The error log history file is
included in Tech
Support Reports.
- Added a graph of detected
potential USB noise that appears when
the hidden debug menu is visible. (Used by OMAX support for
diagnostic purposes.)
- Added tool path verification,
where the calculated tool path is compared with the original vector
data, and if the starting point and ending point of the two data sets
don't agree, an error is generated and logged to the history
file. If the error is more than 0.005" (0.127 mm), then an error
is shown to the operator. Also, if either of the tilt axes do not
return to exactly zero, then an error is recorded to the history file,
and if the error is more than two motor steps (approximately 0.05
degrees), it is displayed to the operator. This verification
always runs on all tool paths, when the software is configured as an
actual OMAX machine tool.
- Improved the Axis Vs. Time
Viewer (a utility supplied in the
applications folder), to allow for better support of viewing of large
tool paths (paths larger than 1,000,000 commands in size), as well as
mouse-wheel zooming.
- Improved exception handling of the tool path interpolator so
that it reports errors that might otherwise cause the compiling process
to lock up.
- Technical Support Reports now include additional information
about USB such as the USB Device Descriptor and Product ID, as well as
more information on concurrently running processes, and more.
- OMAX Tester now reports the USB Product ID in plain sight at
the bottom of the window.
- The user can now prevent Make from automatically closing at
the
end of
automatic reporting if the SHIFT and CTRL keys are held down
simultaneously. This is to allow access to Make for purposes such
as
generating Technical Support Reports, in the event that the automatic
reporting is stopped by an error message or similar.
- It is possible to run a 3D preview of a tool path using the a
hidden menu item in the 3D Path Editor and / or a debug menu item in
Make.
- Contact techsupport@omax.com if you need information
on
any of these.
3D
Path Editor Utility
- Added a new display option for "'Show tilts only for entities
that have tilts", which is now the default display option.
- Added a check box for "Modify connected entities to match
angles"
to the tilt angle specification form. If this box is checked,
then ending angle of the previous entity and the starting angle of the
next entity in the tool path will be set to be equal to the angle of
the entities they touch. This feature is mostly useful as a
shortcut for blending two tangent entities together, but it is not
recommended to use this for non tangent connections.
- When a tool path is opened that contains tilt information, but
the display of tilt angles is not enabled in the viewer, then the 3D
Path Editor will ask if you want to enable display of tilting
information.
- Important: "Purposeful Tilt" is a feature that is
not yet officially supported. Because of the
complexities
involved with the cutting model and hardware, and the extra difficulty
involved in programming for it, it is advised that you do test cuts to
verify the path prior to running on expensive material. OMAX does
not yet advertise machines to have this capability. At this
point, please consider this to be a bonus feature to use at your own
risk. Check www.omax.com/support for updates.
Abrasivejet
Feed Rate Calculator
(Discontinued)
- The Abrasivejet Feed Rate
Calculator has
been discontinued. Nearly all of
it's functionality is
available within OMAX Make, making the feed rate calculator
redundant. For reports similar to those made by the
calculator, use the custom report template "Linear Feed Rate Report" in
Make.
OMAX
Video Player
(Discontinued)
- The OMAX Video Player (and associated media) is no longer
included on software CD's or DVD's and has been discontinued. For
images and other marketing materials, please contact OMAX Marketing
directly.
OMAX
Calculator
- Functions atan, acosh, acos, asinh, asin, and sqr can all now also be typed in as
arctan, arccosh, arccos, arcsinh, arcsin, and sqrt. This helps eliminate
potential user mistakes where the official spelling is forgotten, by
allowing these common alternate spellings. This change affects all
areas where the calculator engine is used, which is nearly all areas of
the software where a number can be entered.
- Display of result is now green instead of red.
New Utility: Tilt-A-Jet Precision
Calibration Software
- This application is used,
along with special calibration hardware, to very precisely calibrate
Tilt-A-Jets. If you have a Tilt-A-Jet equipped machine, this
utility can greatly increase its accuracy by mapping the hardware at
the full range of tilt angles. This is important when using
the "Tilt Forward" feature to speed up cutting, because when tilting
forward the high angle of attack amplifies small errors that might
otherwise be present. This utility requires special hardware to
automate the process. Contact OMAX Technical Support for
information on having the calibration process performed on your
machine, or on renting or purchasing the calibration hardware.
OMAX Technical Support can also assist you in evaluating the need for
such service by cutting a special test part and measuring the results.
Installation
program
- The installer now properly handles the file type association
dialog when installing on Windows Vista, eliminating the need for a
special menu item in Layout to do this.
- Improved progress bar for file copy in Windows Vista slightly.
- Added Tilt-A-Jet Precision Calibration Software to the
installer (shows on the "Start" menu).
OMAX
Interactive Reference
- Lots of new content has been
added, including
- More technical articles
- Large software troubleshooting section
- Developer's Guide
- Information on new and updated features
Bug
Fixes
- Fixed a bug
that could cause the spacing between nested paths to be incorrect when
in units other than "inches" in the array nesting feature.
- Fixed some
tool path font so that the "+" character would properly display.
- Fixed a bug
that could cause Adobe Illustrator AI files to not open, if an AI file
was previously opened in the same instance of Layout.
- Fixed a bug
that could cause an access violation when opening the "File/Open"
dialog if a bookmark referred to a disk drive that no longer exists.
- Fixed a bug
where the "gap length" in the "tab" command would revert back to the
default value after Layout is closed and re-opened.
- Fixed a bug
that could cause an exception error when generating a Tech
Support Report in Windows Vista if certain kinds of disk drives are
attached and no media is in them.
- Fixed a bug
that could cause warnings relating to tiny arcs in inside corners not
offsetting properly to show for entities such as rapid traverses or
etches, where the warning is not necessary.
- Fixed a bug
that could cause the cutting Quality of two entities to swap in the
event of using the "Fillet" command to fillet two arcs of different
qualities.
- Fixed a
conflict that could cause a divide by zero error on some computers when
entering in text in the True Type Text dialog, if the computer has
corrupt or bad monitor device drivers installed.
- The number
"7"
has been added to the FutureSign Tool Path Font, fixing a bug where
that number would not properly appear when asked for.
- Fixed a bug
that could cause a partial redraw instead of a full redraw when an
image is loaded for image tracing, and other windows that are in front
of it are closed or moved.
- Fixed a bug
that would incorrectly cause a "zoom extents" when the "function plot"
command is canceled.
- Fixed a bug
that could cause PDF files that contain negative rotation angles of the
paper to generate an error when importing, and then import the vector
portion of the drawing at the wrong rotation, and with the raster
portion rendered as a gray square with no useful geometry visible.
- Fixed a bug
that could cause a "beep" noise in extremely rare instances when using
the "fillet" command.
- Fixed a bug
that could cause the ".zip" extension to disappear from the .zip file
when saving a Technical Support Report, if the user deletes ".zip" from
the file name when saving.
- Fixed a bug
where
if the snap options form were closed, the focus would not be
returned back to the snap toolbar, resulting in incorrect processing of
keyboard input for the next key press.
- Fixed a bug
that could cause
incorrect tangency when using the SHIFT key to force drawing a line
that is perpendicular to an arc but constrained to a specific
angle. Note that the "rubber banding" may not preview exactly
correctly, but the resulting geometry is perfect.
- Removed some
flicker that otherwise occurs when canceling the file/import dialog
after launching Layout via
the command line to import a file.
- Fixed a bug
that would prevent the FQ
and BQ suffixes in Tool Path Font names to be ignored.
- Fixed a bug
that would prevent the dialog
asking for "number of copies" from showing up, if the "Copy" command
was used with the "Specify XY" snap, and the user had the option "Keep
tool active" turned on.
- Fixed a bug
that could cause a beep
noise when saving a tool path in some rare situations
- Fixed a bug
that could cause some
intersections to not divide with the "Divide all elements touching an
element" and "Divide all selected elements", in the event that the
intersection of two entities happened to be at the end of one of the
entities
- Fixed a bug
that
could prevent pages other than the very first page of a PDF file from
importing properly
- Fixed a
bug that
could cause lead ins to offset when they should not, resulting in a
potential minor blemish at some rare lead locations.
- Fixed a bug that would cause the tool offset to be saved
along
with the geometry data if the "Save as DXF" option is used in the array
nester.
- Fixed a bug that could cause an entity to inappropriately
"divide" itself when
another line is drawn under just the right "magic numbers" conditions.
- Fixed a bug that could cause the Parametric Shape
dialog to lock-up if there was a comma missing in the variable
declaration section of the parametric file.
- Fixed a bug that
could cause unrecognized layers in imported
files from sometimes appearing as "invisible black entities" that are
hard to see.
- Fixed bugs that
could cause PDF or SVG or possibly other files to
not open properly, if a DXF or DWG file was loaded at some earlier
date,
and that file had a non-standard "Layout" chosen.
- Fixed a bug that would prevent entering in of some valid
dimensions
into a Parametric Shape, if
units other than "inches" are selected, and the particular parametric
shape had variables that were declared with a limited range of allowed
values.
- Fixed a bug that could cause a "slit" to offset by mistake if
connected to a Heads
Up Traverse.
- Fixed a bug that
would show the "Specify Length and
Angle" dialog after using the "Perpendicular" snap, which creates an
ambiguous situation with infinite possible results. (So now the
form does not show if the first snap is "Perpendicular"
- Fixed a bug that could cause the origin to be shifted if the
"move drawing onto
grid
if not already there" check-box is "unchecked" and the drawing is then
re-sized for metric automatically during "File / Import from Other
CAD" importing
- Fixed a bug that
would prevent a white dot from being drawn at the division point when
using the "divide" command with the "intersection" snap in certain
circumstances.
- Fixed a bug that
could cause entities to be divided
when they should not be, and divided in the wrong spot, when drawing
other entities near to them. This could cause the symptom of
where you draw something and a nearby entity "bends" over and touches
where you clicked.
- Fixed a bug that
would cause the cursor to be incorrect
when using the "None" snap
- Fixed a bug that
would cause line to arc intersections to not
always divide both entities that intersect when using the various
"intersection divide" commands.
- Fixed a bug that would cause line to arc intersections to not
calculate precisely in certain circumstances. This bug fix could
effect all OMAX applications
- Fixed a bug that
would cause slit qualities to incorrectly
"offset" if the "offset leads" option was turned on, and the slits were
connected to leads.
- Fixed a bug where the "Create Report for Technical Support"
feature, when running
on Windows Vista, might not
include one of the INI files in the Rich Text File report, or in some
cases, might even include an older version.
- Bug Fixes in Make
- Fixed a bug
that could incorrectly allow the next path to start if using "step and
repeat" cutting to run multiple paths, and the "pause at END of next
traverse" command was invoked prior to the very last traverse in the
path.
- Fixed a bug
that could cause the spacing between nested paths to be
incorrect when in units other than "inches" in the array nesting
feature.
- Fixed a bug
that could cause an access violation when opening the
"Change Path Setup" dialog if a bookmark referred to a disk drive that
no
longer exists.
- Fixed a bug
that could cause an exception error when generating a Tech Support
Report in Windows Vista if certain kinds of disk drives are attached
and no media is in them.
- Fixed a bug
that could cause an error message when compiling tool paths where the
Z1 coordinate of the first entity in the path is not zero.
- Fixed a bug
that could cause entities to "weld" together (remove the "dot") when
they should not, during automatic cleaning of OMX files on loading for
files that contained purposeful tilt.
- Fixed a bug
that could cause rough motor motions under certain circumstances if
backlash compensation is enabled
- Fixed a bug
that could cause the progress bar to flicker to 25% for a brief moment
at the end of a tool path compile
- Fixed a very
rare bug in the interpolator that could cause the cutting speed to be
faster than commanded, resulting in a rougher edge than desired, and
possibly a "stuck part"
- Fixed a very
rare bug
that could cause the jet to turn on during a "go to spot on path" move
for machines equipped with Terrain Followers if the terrain follower
was turned on during a previous cut-off-saw command, and the machine is
configured for low pressure piercing and brittle materials.
- Fixed a bug
that could cause the "fastest speed when cutting" value as reported in
the statistics window to be miss reported as a value higher than actual
in some cases for Tilt-A-Jet equipped machines.
- Fixed a bug
that would cause the "limit" snap in the measure command to incorrectly
report the offset path dimensions when the part dimensions were
requested.
- Fixed a bug
that could cause the very last entity of a tool path to not be
considered in the estimated times.
- Fixed a rare
bug where clicking on the "Change Path Setup" button, or pressing the
"Enter" key moments after a part starts compiling could cause part path
corruption due to improperly canceling the previous path calculation.
- Miscellaneous
bugs have been fixed relating to the not yet officially released
"purposeful tilt" feature, to improve the results of parts cut with
this feature.
- Fixed a bug
that would allow the operator to use the "step jog" mode to step past
soft limits.
- Fixed a bug
that could cause the "green numbers" to quit responding in extremely
rare circumstances - even though normal machine motion would still work.
- Fixed a bug
that could cause a rare "timed out" message when a user repeatedly and
quickly pressed jog keys.
- Fixed a bug
that could cause the ".zip" extension to disappear from the
.zip file when saving a Technical Support Report, if the user deletes
".zip" from the file name when saving.
- Fixed a bug where an inside corner could be
mislabeled as "external", resulting in a potential tool offset error.
- Fixed a bug
that forced huge multi-second
delays between motions when automatically squaring the
Tilt-A-Jet. The result of this bug fix means that the squaring
process is now a LOT faster. This same bug fix also improves
response of other motions such as jogging slightly.
- Fixed a bug
that would sometimes cause XY
motion to not start or complete prematurely when the "Move Z Axis up
prior to going home" feature was enabled.
- Fixed a bug
that would incorrectly swap out
"Slit" Quality of "Minimum Taper" with the substitution Quality
specified in the Advanced Setup page, when in fact the Min Taper
Quality should be preserved for slits, since a TAJ can't compensate for
taper on slits (Because there is no "scrap" to tilt into; therefore, it
is necessary to slow down to reduce taper, not tilt.)
- Fixed a bug
that could potentially cause
a minor squareness issue on parts with the Tilt-A-Jet during operations
at high tilt angles (though results of this "bug" have not been
observed on actual parts.)
- Fixed a bug
in
the Interpolator that
would incorrectly restrict how quickly the Tilt-A-Jet would respond to
fast changes in tilt angle.
- Fixed a bug
that would cause the jerk
filters to slow down more than necessary on arcs inserted as part of
the tool offsetting.
- Fixed a bug
that would allow a user to
right-click on the title bar of the Z axis tool bar, and choose
"maximize"
- Fixed a bug
that could cause an incorrect
deceleration profile to be used when jogging the Z axis.
- Fixed a bug
that could incorrectly set the
size of limits of travel for Fabricator machines that are extended
longer than the default length.
- Fixed a bug
that
could cause a "beep" noise when jogging a machine, if an OMAX USB box
is
plugged in, but Make is
configured as an off-line PC.
- Fixed a rare
bug
that could cause an
error of a single motor step at heads up traverses
- Fixed a rare
bug that could cause tool
path calculations to lock up for parts that contain heads up traverses.
- Fixed a
bug that
could cause lead ins to offset when they should not, resulting in a
potential minor blemish at some rare lead locations.
- Fixed a bug
that
could cause the nozzle to open during a traverse when using low
pressure and a constant speed pump.
- Fixed a bug that
could cause some corner passes to not occur when they should on corners
defined by one or more arcs.
- Fixed a bug in the preview
command "Show Path Sequence" where the very first event shown
was numbered "2" instead of "1".
- Fixed a bug that
could cause the Z axis to "drift" if Heads Up Traverses were used in
combination with the Tilt-A-Jet
- Changed the email server used by the Tech Support Report
Email
feature
to a more reliable server that hopefully will not change for a very
long time.
- Fixed a bug that would cause the tool offset to be saved
along
with the geometry data if the "Save as DXF" option is used in the array
nester.
- Fixed a bug in interpolation that could cause a tiny amount
of
Tilt-A-Jet
"drift" if certain geometrical combinations were repeated over and over
in combination with using Heads up Traverses. This bug would most
frequently show up when Leads are not used to pierce the material.
- Fixed a bug that could cause the Parametric Shape
dialog to lock-up if there was a comma missing in the variable
declaration section of the parametric file.
- Fixed a bug that
could cause an "AskFor" variable to not get "asked for" when a report
is generated that has only a single "AskFor" variable in it.
- Fixed a bug that
could cause a sudden acceleration at the point of intersection between
a lead and a Heads Up Traverse, if the lead and traverse were exactly
tangent to each other, and a very high machineability is used.
- Fixed a bug that
could cause a lock-up during compiling if a distance of exactly 2.5" is
specified for the Heads Up Traverse "hop distance".
- Fixed a bug that
could cause an "Access Violation" error when generating a custom report.
- Fixed a bug that
could allow Z1 or Z2 signals to be sent even if no Z axis is attached,
if the "Page up" or "Page Down" keys were pressed.
- Fixed a bug that would prevent entering in of some valid
dimensions
into a Parametric Shape, if
units other than "inches" are selected, and the particular parametric
shape had variables that were declared with a limited range of allowed
values.
- Fixed a bug that could cause a "slit" to offset by mistake if
connected to a Heads
Up Traverse.
- Fixed a bug that
would cause an error "cannot focus a disabled or invisible window" if a
tool path finishes compiling while the "About" box is showing in Make.
- Fixed a bug that
would cause slit qualities to incorrectly
"offset" if the "offset leads" option was turned on, and the slits were
connected to leads.
- Fixed a bug where the "Create Report for Technical Support"
feature, when running
on Windows Vista, might not
include one of the INI files in the Rich Text File report, or in some
cases, might even include an older version.
- Other bug fixes
- Fixed a bug
that could cause non-English versions of Watcher and Make to not properly
communicate the status of whether make is running a path or not, and
thus cause the "pause" button in Watcher to be grayed out when it
should otherwise be available.
- Added extra
error trapping in the "Create Report For Tech Support" feature to
prevent a potential exception error when listing disk drives in Windows
Vista.
- Fixed a bug
in
the 3D Path Editor that could
cause the display to lock up if the "Set eye target" command was used
to set the target to a location in the 3D window when no path was
loaded.
- Fixed a bug
in
a low-level routine that is used in many OMAX applications for
determining the angle between two entities that could sometimes return
an
incorrect angle. Though this bug was not known to cause any
specific issues, the fact that it is fixed may eliminate rare but
unknown bugs through the software.
- Fixed a bug
in
both Layout and Make that would cause the extension ".zip" to go
missing from Tech Support Reports if the user deletes it from the
file/save dialog.
- Fixed a bug
in
the 3D Path Editor that would
cause numbers entered into the "Reference Geometry" form from being
correct when switching between mm, inches, or cm.
- Fixed a bug in all
applications
that could cause numerical expressions entered into edit boxes to be
incorrect in in the case of certain trig functions (Sin, cos, etc.)
resulting in negative numbers being subtracted from the rest of the
expression.
- Fixed a bug
in
Link.exe (a utility used by the help
screens) that could cause links to external applications to not
load properly on Windows Vista.
- Fixed a mislabel of the "TY" check-box in the Axis vs Time viewer diagnostic
utility.
- Fixed a bug that can cause the various OMAX software
applications
to lock if currently logged in user does not have sufficient privileges
to write to the disk. Now, an error message appears in its place.
- Fixed a bug in OMAX Tester
that would display a red triangle on a "Send" button, when it should
not be there.
- Fixed a bug in All OMAX
Applications that could cause some extremely large radius arcs
to not display when zoomed in to high magnification.
- Fixed a bug that could cause the wrong Z coordinate to change
when a Z1 or Z2 coordinate is moved after the "Mirror X" or "Mirror Y"
command is used in the 3D Path Editor.
Rev
11.0
Changes made
since rev "10.0" of the software, which was
released 12/11/2006.
Special
Changes to support Windows
Vista
- Lots of changes have
been
made to properly support Windows
Vista, without introducing headaches to users in older operating
systems. Most of these changes should be completely transparent
to all users, though significant changes have been made "under the
hood" to accomplish this.
- License Registration: License
registration has
been updated to work within Windows Vista security. This prevents
a problem where Vista would "un-register" the software, and create
application errors periodically.
Location of setup and
common files: In Windows Vista, setup files for the OMAX
software are moved to a location that can be accessed by all Vista
user's, allowing different people to share the computer with different
log-ins, yet keep the same software setup settings and share
data. (Which allows the machine setup to be preserved, even if
different users log in.) These files are in the "C:\Users\Public\OMAX_Corporation\AllUserData\"
folder and its sub folders, where in XP and 2000 these same files are
kept in C:\Program Files\OMAX Corporation\OMAX_Layout_and_Make\, as
they have always been.
- Installation and
updating of device drivers has been updated to properly work on
Vista
- Code has changed to properly execute the "Cooler
Control"
application on Windows Startup, if configured to do so
- File type associations
now work properly (so you can associate DXF, DWG and ORD files to open
in OMAX software when double clicked on, if desired.)
Note: In
Windows Vista, file associations are set from within the "File /
Register File Associations..." menu item in Layout, Make, or the 3D
path Editor - NOT during the
installer process. Therefore, if you want your DXF, ORD,
or OMX files to open in OMAX software when double clicked on, be sure
to run this command in Layout. In XP and 2000, file type
registration is done
during the software install process. Note also that once they are
set, there is no "un-register"
capability. If you wish to change the registration to a different
application, then it is necessary to use that applications "register"
features, or use the file registration tools built into the operating
system.
- Many other minor changes
have been made that listed individually would be
impractical to list in this document, but cumulatively add up to a
proper
Vista compatible experience.
- For additional Windows
Vista related information, visit the OMAX Technical Support web
site (http://www.omax.com/support)
Layout
- Changes and additions to the "Import from
other CAD" command:
Added new capability to read "DWF"
files.
Added capability to read and decompose PDF
files.
- Important Notes:
- PDF files are not meant
to
be decomposed for editing in CAD software. In fact, they are
designed to prevent being edited, and they are designed to be viewed on
the screen or printed. Therefore, PDF files are NOT preferred methods
for importing into the OMAX software, and they will likely contain
features not appropriate for cutting, as well as inaccuracies.
Use them with caution, and expect to have to do some clean-up after
importing.
- PDF images are a mix of
vector and raster data. Some images might not contain any
vector data at all. In this case, the OMAX software simply brings
it in as a bitmap for the user to trace "by hand" or trace using
"Intelli-TRACE". Vector portions of the file import as lines and arcs,
and the raster portion imports as a bitmap background the same bitmap
background used for image tracing.
- PDF files do not
necessarily contain vector data. In fact, many PDF files don't
contain any vector data at all. In this case, Layout will only import
the bitmap background, because that is all there is available to import.
- The bitmap image of the
PDF is automatically darkened to 50% brightness when it is loaded.
This makes it easier to see the vector data on top of it. If
brightness other than 50% is preferred, use the Image Tracing "Adjust
image colors"
command to set it otherwise.
- The actual size of the
bitmap image (its resolution) depends on the memory and speed of your
computer. On a a really fast high memory computer, Layout
may render the bitmap up to 30 megapixels in size, if there is less
memory or speed available, the image will be a lower resolution.
Basically,
it is re-sized it so that it "zooms" reasonably quickly, yet has enough
resolution so the user can see it clearly. It is also sized so that if
the user decides to run Intelli-TRACE, it does not bog down too much.
Note that the Image Resolution setting used by the Image Tracing
feature in Layout will automatically be set to the value appropriate
for the PDF file, so that the bitmap image of the PDF file will line up
precisely with the vector data it also contains.
- Although it is
technically
possible to have a PDF file that is reasonably high precision, most
PDFs are not. For example, many PDF files are created using a
"virtual printer", which tends to create low resolution PDFs. Circles
will likely not import as true circles, for example, but instead may
look like warped polygons. This is a fault of the PDF itself, and
not the PDF translation. If you need precision, use DXF. If you
have no choice but to use PDF, then consider rendering the PDF file to
a large paper size (Such as A0, 32"x44" or similar), which will
improve the precision slightly compared rendering to smaller paper
sizes.
- Most standard text is not
converted, but instead left in raster format. This is
something left for future development, if
there is customer demand. (If you think this is something OMAX should
supply and is worth doing, email techsupport@omax.com to
request this feature.)
- PDF files may contain
more
than one page. If a PDF has multiple pages, then Layout will ask
which page to import.
Added
support for a new "Generation" of IGES
/ IGS file import filters.
- The old filters are still available to insure backwards
compatibility, but the new ones offer
considerably better support.
- The same dialog as the "DXF/DWG" file import filters now
displays when importing an IGS or IGES file, though the configuration
options are limited.
- Important: Although
we went to considerable effort to add this extended support for
IGES/IGS files, it is still the case that not all IGES files are
supported. 3D IGES files usually will not import - use 2D files
only. In addition, as with DXF and DWG, there are many different
"flavors" of IGES
that do not adhere to proper IGES standards. These also may not
import properly. It is suggested that you use DXF or DWG for your
file sharing needs, and only use IGES if you do not have any
choice. If you have 2D IGES/IGS files that do not import
properly, we would love to use them for testing. Please send them
to techsupport@omax.com.
- Improvements have been
made
to the DXF / DWG file import
filters, in particular relating to reading AutoCAD 2007 files.
- Important: At this
point, some AutoCAD 2007 DXF or DWG files may still not import
properly. If you need to convert version 2007 DWG files to
version 2006 or older, in order to import them into Layout, then you
have these choices:
- Open the file in AutoCAD 2007, and re-save as an older
version
- Use the free utility from Autodesk, DWG
TrueConvert, to "down convert" the file prior to importing into
Layout.
- Ask your customer to send you the file as an older style
DXF/DWG
- Wait for future free software updates from OMAX that will
include additional support for version 2007 files.
- There is a new option to "Move
drawing onto
'grid' if not already there", when importing DXF, DWG, or IGES
files. so it is now possible to keep the exact original coordinates
from the original CAD system, if desired (Un-check the option to
preserve original coordinates.) In older software, this option
was always on - now you have the choice.
- As always, if you have a
file
that does not import properly
into the OMAX software, please email it to techsupport@omax.com,
so that we may use it to improve
our file
filters for the future. Ideally, include the original file, and
let us know what CAD program it came from originally, and details on
what is wrong.
- Array Nester: Added
"Center" as an option for the Start and End points of the tool path
when using the Array Nester.
- Increased the default resolution for the "Redraw as Solid"
slightly to improve the amount of resolvable detail slightly when
rendering on Windows XP.
- Technical Support Report now displays additional information
about
monitors attached to the computer (useful for multi-monitor setups.),
as well as some additional language information.
- Added a new Tool Path Font
"Capsule Chain" which is essentially the same font as "Capsule"
with different caps on the end, making it useful to make bracelets
connected with chains. Capsule and Capsule Chain fonts have also
had the letters A-Z and a-z and numbers 0-9 optimized to work with tool
offsets of up to 0.029", which means the letters can also be shrunk
down smaller before tool offset errors occur.
- Hold down the Shift key when clicking on the "Render as
Solid"
button
for a material usage estimate. Note: This feature is not
officially
released yet, which is why it is hidden.
Make
- Array Nester: Added
"Center" as an option for the Start and End points of the tool path
when using the Array Nester.
- Added "Pierce Safety Factor
for
Low Pressure Piercing" to the Advanced / Administrator
setup. This allows adjusting the pierce safety factor separately
for low and high pressures, for a finer level of control than
previous. The default low pressure pierce safety factor is set to
1.3x, which allows considerably more margin for error for low pressure
piercing, resulting in more reliable piercing at low pressures with
less risk of cracking by preventing the high pressure from kicking in
too early.
- Resuming a tool path using the
"Go to Spot on Path" command, and a Heads Up Traverse is chosen
to go to, or if the Z axis is otherwise at a different height than the
tool path should be at, then a message will ask the user if it is ok to
move in the Z direction to find the correct height for resuming.
If "Yes" is chosen, then the Z axis will move to the location, if
"Cancel" is chosen, then the Z axis will stay where it is, and the path
will resume at whatever Z height it happens to be at.
- Dual Z Axis support change: Changed
the Z axis coordinate display so that the "Zero" and "Go" buttons now
lock together in sync with the buttons on the Z axis toolbar.
This helps prevent accidentally moving an individual Z axis when they
are locked together.
Support for "Programmable Tilt":
It is now possible to program in purposeful tilt angles for an entire
part, or on a feature by feature basis within the tool path. In
order to do this, it is necessary to do one of the following:
- Use the OMAX 3D Path editor to assign tilt angles on
individual
drawing entities in an existing tool path. (See 3D Path Editor
information below)
- Hand-edit a .OMX file to enter in tilt angles for the
features
that require it. (Consult the help screens for information on the
OMX file format, and its structure)
- Use a 3rd party 3D editor such as Mastercam to output the 3D
information. (Mastercam now has a 3D Post Processor for the
OMAX. Contact tech support
for details and availability.) Other 3D CAD/CAM systems can also
work, consult the 3rd party software reference guide in the OMAX
Interactive Reference for details.
- Simply enter in a non-zero number for the "Taper Offset"
value
in Make (In this case, assigning tilt to the entire part.)
- Important: This
feature is new, and not officially supported yet. Because of the
complexities
involved with the cutting model and hardware, and the extra difficulty
involved in programming for it, it is advised that you do test cuts to
verify the path prior to running on expensive material. OMAX does
not yet advertise machines to have this capability. At this
point, please consider this to be a bonus feature to use at your own
risk.
Added support for the "Pull To Open Valve"
high pressure valve. This valve increases reliability when
piercing brittle materials, and required some minor non-visible
software changes in order to work at it's best.
Completely
re-worked the Terrain Follower
code (For optional Terrain Follower accessory):
- Terrain follower is
always either in the "Off" our "Auto" mode, and the controls for it
have moved to the "Change Path Setup" dialog. (A single check box to
enable or disable it for the path.)
- "Hard Pause" settings: Added
slider bars in the "Advanced / Administrator Setup"
dialog that determine how hard to decelerate in the event the Terrain
Follower detects a collision. This allows the machine to come to
a very fast and abrupt pause in the event of a collision, instead of
the normal smooth slow deceleration that is inappropriate in the event
of a collision.
- Added support for automatically
setting the stand-off by
holding down the "Stand-Off" button on the Z axis toolbar. Simply
move your nozzle over the material, and then hold down the "Stand-Off"
button until it touches. It does not require that the Terrain
Follower be enabled, in order to work. This can be useful, even if you
intend
to have the Terrain Follower disabled for the path itself.
- Z axis display now resets to
your default stand-off value when the terrain follower is
in use, and also displays as "Auto" to prevent user confusion that was
caused by having the numbers change. So, if you use the
"Stand-Off" button to automatically set your stand-off, then the value
displayed in the Z axis number display will reflect the stand-off value
set as the default preference in the "Motion Preferences"
dialog. Note: It is important that this value match the
actual stand-off value that the Terrain Follower is calibrated to, or
else the software and hardware will be out of sync.
- Added a check-box to enable
or
disable the Terrain Follower
during a "Vector Move", or "Cut off Saw" operation. (Defaults
to "off")
- Added code to better handle
the Terrain Follower being on with
paths that have "Heads up Traverses" in them. Note that
the
"Backup" feature will be disabled when using the Terrain Follower on
paths that have the Terrain Follower enabled and Heads up Traverses in
them. Use the "Go to Spot on Path" command if you need to go
backwards in such a path. Note also that there are delays between
when you press the "Backup" or "Ahead" buttons and when the X,Y motions
actually start to happen. These delays are there to insure that
the Terrain Follower has adequate time to follow the material from
whatever position it is currently at.
- Know if it's enabled: If
the Terrain Follower is enabled, it says so at the very bottom of the
"Statistics" display
- Reminder to calibrate: If
the terrain follower is attached, and Make is configured to warn users
about the need to "Home" the machine, then the message displayed will
also remind the user to calibrate the Terrain Follower stand-off, in
case it has drifted over time.
- Support for Tilt-A-Jet's:
The Terrain follower now works with the OMAX Tilt-A-Jet
accessory. Note: If doing precision work that is beyond the
advertised specification for the machine, (say, 0.002" or better)
and/or when doing work with high angles of tilt, it is recommended to
use a feeler gauge to get the stand-off distance "perfect", and disable
the Terrain Follower for that part, and to cut on flat material.
- It is no longer allowed to
use
the "Page Up" or "Page Down" keys (or any other Z keys) to move
the Z axis while the terrain follower is active. (This prevents a
conflict that was overlooked in previous releases.)
- If a path contains 3D
information (other than "Heads up Traverses") that move more
than 0.1" (2.54mm), then turning on the Terrain Follower is not an
option. (Because it will conflict)
- If the "Go To Spot On Path"
feature is used, the machine will traverse into position, but
will not lower down to the
height for cutting until the "Continue", "Ahead", or "Backup" buttons
are pressed.
- If "Move X", "Move Y",
"Move
Radius and Angle", "Go Home", or "Go to X,Y coordinate" are
used, then the Terrain Follower will NOT drop and follow during these
actions. This is to prevent the case where the user may have had
the head in the air in order to clear obstacles, where it would be
unwise to "follow" the material and crash into them. (Note: The
"Move Radius and Angle" command has the option of turning on the
Terrain Follower, if desired.)
- The "Cut Off Saw" command
has
a check-box making the Terrain Follower optional for this
operation. By default it is turned OFF, because the Cut Off Saw
command is often used to cut materials starting from the edge, where
the Terrain Follower may otherwise snag.
- Added additional machine types
to the choices in the Advanced / Administrator Setup dialog, to
accommodate many new machines now available from OMAX. So the
list is now:
- OMAX 2626
- OMAX 2626xp
- OMAX 2448
- OMAX 2652
- OMAX 2652a
- OMAX 55100
- OMAX 6060 (new!)
- OMAX 80160
- OMAX 60120 (new!)
- OMAX Fabricator+0m (new!)
- OMAX Fabricator+2m (new!)
- OMAX Fabricator+4m (new!)
- OMAX Fabricator+6m (new!)
- OMAX Fabricator+8m (new!)
Check with OMAX
sales or omax.com for
specifications and availability of new machines.
Improved "Time Remaining"
display when running paths: The estimated Time Remaining
display in the Path
Controller dialog no longer
grays out and becomes invalid after using the Dry Run or "Backup" or
"Ahead" or "Go to Spot on Path" features. The times are now
correct.
Support for dual abrasive flow rates
(requires optional hardware): Added support for the "low" check-box to
turn on the low pressure
bit when doing an abrasive test to the "Test Pump and Nozzle"
dialog. This allows for easy measurement of the low abrasive flow
rate setting when using a machine equipped with dual abrasive flow rate capability.
- Added warning to the "Test
Pump
and Nozzle" dialog to warn about the danger to the bottom of the
tank of firing the nozzle
for extended periods of time with the nozzle above the water
level. (This can quickly cut a hole in the bottom of the tank,
because the entrained air creates an "air bearing" that allows the jet
to be effective all the way to the bottom, where it picks up abrasive
and erodes away.)
- Added "Drill accessory is
attached" check-box to the Advanced Administrator Setup, to
enable the drill accessory without the requirement to install special
software.
- Technical Support Report now displays additional information
about monitors attached to the computer (useful for multi-monitor
setups.), as well as some additional language information.
- Hold down the Shift key when clicking on the "Render as Solid"
button for a material usage estimate. Note: This feature
is not officially released yet, which is why it is hidden.
3D Path
Editor Utility
Support for viewing tool paths with
purposeful Tilt: Paths that have purposeful tilt assigned to
them will display with the tilt showing in the 3D path editor, with a
new display option.
- Display options relating to tilt are on a new "Tilt View
Settings" pull-down menu.
- Tilt shows up as tilted entities with a color representing
the magnitude and direction of the tilt. Left-hand tilting is
colored orange, while right hand tilting is sky blue.
- Tilt can be exaggerated in the view, so small tilt angles
are
easy to see.
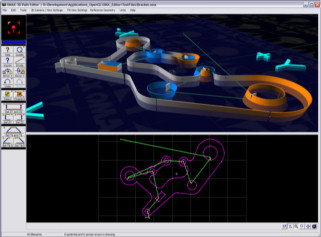
Above: A typical part with
tilt assignments shown in blue and orange color
Support for modifying tilt on a per-entity
basis: 3 new buttons have been added to allow setting the
Starting Tilt Angle, and the Ending Tilt Angle for each entity in the
tool path. These 3 buttons work essentially in the same way as
for setting the Z heights. The keyboard equivalent for setting
taper on selected entities is "T"
- A new menu item has been added for "Set maximum allowed tilt", which
sets the largest tilt angle the software will allow. Be sure to
set this value to a value less than or equal to the maximum tilt
allowed by your particular Tilt-A-Jet accessory.
- The keyboard equivalent for
changing the camera's target location has changed from "T" (for
"Target") to "E" (for "Eye Target"), in order to free up the "T"
key to become the keyboard equivalent for the new "Taper" command.
- Important: This
feature is new, and not officially supported yet. Because of the
complexities
involved with the cutting model and hardware, and the extra difficulty
involved in programming for it, it is advised that you do test cuts to
verify the path prior to running on expensive material. OMAX does
not yet advertise machines to have this capability. At this
point, please consider this to be a bonus feature to use at your own
risk.
International
Languages
- In addition to English,
German, French, Italian, Spanish, and Polish, which were
released in
version 10, there is now support for Chinese
and Japanese. Download from the OMAX
Technical Support web site, or order on CD or DVD.
Software Installer
- Software installers and some key files are now "Digitally
signed" by the independent company VeriSign
for security and validation purposes. One feature of this is that
it allows the person installing the software to be assured that the
software came from OMAX.
- Added extra code to prevent some dialogs from appearing
during
the un-install process that should not be there.
- Significant changes have been made in order to support Windows
Vista.
- Removed "Modify" and
"Repair"
options from the installer
because these have the opportunity to otherwise corrupt the
installation.
- Easier to install
accessories: Removed the requirement for separate installation
CD's in
order
to activate the Precision Optical Locator, Drill, Motorized Z axis, or
Tilt-A-Jet accessories. Note that separate CD's or configuration
disks may still be needed in order to install necessary device drivers
or configuration files (which is the case for the Tilt-A-Jet and
Precision Optical Locator accessories.)
Special Changes to
USB Card Firmware
- Two changes have been made
to
the firmware to make the USB Card more resistant to noise.
Now, when no other OMAX applications are running, the card is sending
data to shut off all OMAX devices 100 times per second. When Make
is running, the proper relay data for the operation at hand is sent
about 50 times per second. This insures that electrical noise can
not start and run or stop OMAX equipment except when it is supposed to
be running or stopped.
- Additional changes have been made to the firmware. For
details read the "readme.txt" file located in the "Drivers" folder of
the OMAX Software CD or DVD.
Bug
Fixes
- Fixed a bug in Make that could cause it to mis-report tool
offset
errors when no tool offset errors actually occurred in tool paths where
corner passing is enabled.
- Fixed a bug in Make where corner passes on arcs could sometimes
cause tool offset errors.
- Fixed a bug in OMAX Camera that could cause OMAX Camera to
disappear behind Make sometimes.
- Added code that significantly increases the reliability of USB
communication between the OMAX USB box and the computer. In
particular, it makes Make more tolerant to slow data transmissions that
can occur when noise is present.
- Fixed a bug that could allow the user to use the "continue from
path interrupted home" after re-zero-ing to a new "path start home"
that is different from where the previous path was started.
- Fixed a bug that could occur "beeps" to occur during some
keyboard commands.
- Fixed a bug that could cause the rotation and "flip" state of a
part to flip differently when the tool path is compiled than what was
previewed in the "Change Path Setup" dialog.
- Fixed a bug that could cause a "soft limits will be exceeded"
message to incorrectly display when it should not, when using the "go
to spot on path" or "continue from Path Interrupted Home" commands.
- A bug was fixed in the firmware of the OMAX USB device that
could
cause an error of +/- one motor step when pausing the machine while
running a part. This error would be +/-0.0005" on most OMAX
machines, or +/- 0.00025" on OMAX 2626xp
machines. This bug is now fixed, and after installing version 11
of the software the fix will automatically be applied to the OMAX USB
device firmware
after re-booting the computer.
- Fixed a bug in Layout that could cause the "Preview after
generating a tool path" dialog from displaying properly on some
multi-monitor systems, as well as a similar issue with the "File /
Open" command.
- Fixed a bug that could cause "Mirror about a line" command to
not
work if "erase original" was checked
- Fixed a bug that could corrupt the undo buffer when using the
"Mirror about a line" command
- Fixed a bug that could cause the angle automatically filled in
for the "Rotate Copy" command to not always auto-fill
- Corrected some code in the tool path interpolator that never
surfaced as any known bug, but might some day
- Fixed a bug in the Terrain Follower code that could cause the
Terrain Follower to move up in Z slightly if the "Ahead" or "Backup"
keys were very rapidly clicked.
- Fixed a bug in the installer that prevented the firmware on the
OMAX USB device to not properly update when upgrading over version 4 or
older of the OMAX software.
- Fixed a bug that could cause some binary DXF files to not load
properly with the Generation IV DXF file filters.
- Fixed a cosmetic bug in Make that could cause long leads to not
be drawn to the screen at certain magnifications
- Fixed a bug in Make that could allow the user to move Z1
independent of Z2, even if the "Lock Zs" check box were checked, if the
numeric keypad was used to move the Z's.
- Fixed a bug that could cause "AskFor" variables in custom
reports
to be ignored if there were only a single "AskFor" variable in the
report.
- Fixed a bug that could cause improper operation of the Pull to
Open Valve on the first pierce of a tool path.
Rev
10.0
Changes made
since rev "9.0" of the software, which was
released 6/27/2006.
International
Languages
- The OMAX software is now
available in a variety of languages including:
- English
- German
- French
- Italian
- Spanish
- Polish
- Languages are available as:
Software Installer
- The install program has been
completely
re-done to provide better support for non-English versions of
the OMAX software, as well as to provide more capability and
compatibility for the
future. Great pains were taken to make sure the installation
process remains as simple as possible, given the constraints of the
Microsoft System Installer technology used. Some considerations:
- Installing over older OMAX
software should be easy, and similar to the way it has always
been. Simply run the new installer, and choose all of the
default settings. There is no need to uninstall first.
- The
minimum system requirements for the OMAX software have raised. The installer will not install
the software if you attempt to install on a system that does not meet
certain requirements. See System
Requirements for
details. (Basically, you need Windows 2000 Service Pack 3
or newer, and
1024x768
screen resolution or higher, and 16 bit color or higher. All
Windows based OMAX machines meet this minimum specification, unless
changed.)
- When installing over an older version, in some rare cases,
you
may discover duplicate icons on your
desktop or your start menu.
If this happens, and it bothers you, then simply right-click on the
duplicate, and choose "delete". Otherwise, these duplicated icons
will work fine, and are harmless.
- The Windows "Add / Remove"
dialog will likely contain more than one entry for the OMAX Software.
This does not hurt anything. Future software upgrades will likely
add additional entries to the "Add / Remove" dialog. Again, these
do not hurt anything. When uninstalling, these extra entries can
be removed in most cases by simply running the uninstaller for each
entry. However, it is possible that some entries may stick
around, even after the software has been uninstalled. Again, this
is harmless, but a slight annoyance, and a by-product of a trade off we
made to make the installer (and upgrade) process easier in other areas.
Make
- New variables added to the
custom report generation feature, "[OMAX_JobCostingCostPerHourValue]" and "[OMAX_EstimatedCostValue]", which are the same as
"[OMAX_JobCostingCostPerHour]" and "[OMAX_EstimatedCost]", except that
they do not include the currency symbol, making these variables useful
for calculations in spreadsheets.
- Edit a Custom Report Template
at
the same time as the report is generated. (In other words,
if you are using WordPad to edit the template, you can leave WordPad
open when you test the template, where previously it would generate an
error.) This makes editing and previewing templates faster and
easier.
- "Transfer Settings" wizard now
transfers all settings that can affect the time estimates of the
machine, including installed support software, such as the software for
the Tilt-A-Jet, Motorized Z Axes, and Drill Accessory. It is no
longer necessary to install these CD's separately on an office PC for
precision time estimates. In addition, the wizard will warn when
importing files from a different version of software.
- Support for "Hard Pausing" added, to pause the machine as fast
as
possible, when the baby-sit is triggered. This allows for very
fast, but violent pausing if the hardware pause or baby-sit is
triggered, yet a smooth and pleasing pause speed for other
operations. This "Hard pause" only is enabled if the terrain
follower accessory is installed and turned on, and allows the machine
to stop abruptly in the event of a high speed collision.
More support for advanced "developer"
features:
- Make now broadcasts key
information about its status via "Windows Messaging" so that
other applications can easily pick this information up. This
feature is not documented in the help screens. Contact
techsupport@omax.com, if you are interested in learning more.
- Make now can be run, and a
path can be started, from the command line
(for example launched from a .BAT file, or called from a 3rd party
application). This is for use in automated systems where
user intervention is not desired. This feature is not documented
in the help screens. Contact techsupport@omax.com, if you are
interested in learning more.
- Make can now accept a
Bitstream file (*.bts) from the command line. So, it's
possible to open a BTS file by simply double clicking on it in
explorer, for example. This is useful for running pre calculated
tool paths for special purposes. (BTS files are
to the OMAX as Atoms are to objects, or assembly language is to
software
- they allow extreme control
of the hardware, supporting ultra high resolution positioning and
timing of 8 axes and 16 or more digital outputs, but are also very
difficult
to create. For information on BTS files, contact
techsupport@omax.com, because they are currently not officially
documented.)
Layout
Rudimentary Support for AutoCAD 2007 DXF
and DWG
importing: The "Import from Other CAD" command now can read some DXF
and DWG files that were created in AutoCAD 2007 (Previously, support
only was up to AutoCAD version 2006). Note: This is the first cut
at 2007 support. AutoCAD 2007 support is not as strong as support
for older DXF/DWG versions. Therefore for maximum reliability it
is still
recommended to use older versions of DXF / DWG files when
possible. Also, send any files that give you troubles to
techsupport@omax.com so that we can help you with a fix and
improve our
filters.
Important: At this point,
many AutoCAD 2007 DXF or DWG files will still not import
properly. If you need to convert version 2007 DWG files to
version 2006 or older, in order to import them into Layout, then you
have these choices:
- Open the file in AutoCAD 2007, and re-save as an older version
- Use the free utility from Autodesk, DWG
TrueConvert, to "down convert" the file prior to importing into
Layout.
- Ask your customer to send you the file as an older style
DXF/DWG
- Wait for future free software updates from OMAX that will
include additional support for version 2007 files.
- Other DXF / DWG file importing improvements:
- Importing drawings with
multiple "Layouts": If
a DXF or DWG file being imported has multiple "Layouts" in
it, then the "Layouts" choice in the Import dialog will draw attention
to itself by being highlighted with a yellow border. This is so
that you know that this file may have more than one part specified in
it.
- Some fixes were made to support a few additional "flavors" of
DXF and DWG files.
Lots of new Tool Path Fonts: "RockBar
Connect", "QuickName", "Emboss", "Capsule", "Empower", "Presidential",
"Keyed", and several
"Blazed" fonts
have been
added. These fonts came from other OMAX customers. Note
that you can make your own tool path fonts, and if they
are of high-quality then OMAX would like to consider purchasing them
from you to then include in
future software updates. If this is of interest to you, be sure
to read the topics "Creating your own fonts for Layout", and "Checklist
for submitting fonts to OMAX" in the OMAX Interactive Reference.
- Tool Path Font dialog now
remembers previous folder fonts were loaded from, in the event
that fonts were loaded from a folder other than the default
location. This makes it a little more convenient to develop fonts
in an alternate folder. To restore the default folder, simply
right-click in the font list for a menu of options.
- Create custom color schemes:
In addition to the pre-defined color schemes of "Black", "White",
"Teal", "Extra Bright", etc., it is now possible to mix your own custom
colors. To make your own custom palette: Close all OMAX
software, open "CustomColors.INI" in NotePad or similar, then
re-save it with a new name "Colors.ini", (overwriting existing
Colors.ini file). Make your changes to this file. When you
are ready to test, re-save as "Colors.ini",
run Layout or Make, and then open the Preferences dialog and choose
"From Colors.ini" as the color scheme to use.
3D
Path Editor
- Improved Error reporting on
leads: If there are any Changes in Z along a lead in or a lead
out, then this will always be reported as a "potential error" in the
status bar at the bottom of the screen, and the lead will be
highlighted in the 3D view to make it more visible. This is
because changes in Z over a lead can cause steep angles to occur when
the leads shrink in X and Y as a function of the Intelli-PIERCE
function in Make. (It is still possible to make the leads at
angles in Z, but it is not recommended.)
Other
utilities and general changes
- The "About" box in OMAX Tester now reports Device Driver and
DLL information.
- Email support for the "Create Report for Technical Support"
feature now
uses different technology that is (hopefully) more tolerant of
fire walls and other such things that might otherwise prevent emails
from being sent.
- Lots of minor changes were made to dialogs and menus to make
them easier to translate into other languages
Bug
Fixes
- Fixed a bug in Layout that
could cause the "pixels / inch" scaling property for images being
traced to be incorrect if units other than "inches" were used.
- Fixed a bug in Layout that
could cause an incorrect fillet when filleting between two arcs where
one arc was almost exactly a complete semi-circle, and the fillet
radius was tiny or zero.
- Fixed a bug in OMAX Camera that
could cause the "Zoom" buttons to disappear.
- Fixed a bug in Layout that could cause Layout to lock if the
"Q"
key was held down continuously, and then the "A" key was held down
continuously.
- Fixed a bug in OMAX Calculator
(and
all locations in all other OMAX software where mathematical expressions
are evaluated), that could cause incorrect evaluation of the expression
if negative numbers were used with exponents in certain circumstances.
- Fixed a bug in Make that
could cause an improper compensation by the X and Y axes when tilting
when stand-off distances other than the default value of 0.060" (1.5mm)
were used.
- Fixed a bug in Make that
could cause the stand-off to be
incorrect if the "Page Up" or "Page Down" keys were used to move the
machine after pausing, but before using "go to spot on path".
Also, suppressed an unnecessary warning message in this regard.
- Fixed a bug in Layout that
could cause "slits" to have an offset,
if path with slits in it were saved as an .OMX file.
- Fixed a bug in OMAX Make that
could cause estimated times to be
slower than actual times on tool paths containing heads up traverses
- Fixed a bug in OMAX Watcher that
could cause troubles when
running OMAX Watcher on a computer with non-USA number formats.
- Added additional exception handling code to OMAX Watcher to
provide more reliability on unreliable networks.
- Added additional exception tracking to OMAX Make to track errors
on start-up for easier diagnosis should any occur.
- Make: Fixed a bug that
could cause an improper tool offset on the
last element before a lead out, when using water-only cutting.
- Fixed a bug in Layout that
would cause a "cannot focus disabled
window" error under certain conditions when using the "frame" command.
- Fixed a bug in Make that
could cause an exception error if the
DD/MMM/YY format is chosen in "regional settings" as the method of
displaying dates.
- Fixed bug in Layout that
could cause the "undo" command to "undo"
incorrectly after using the "Mirror X" or "Mirror Y" command several
times in a row.
- Fixed a broken link to the help
screens in the "Advanced /
Administrator Setup" dialog
- Fixed a bug that would cause the video display in OMAX Watcher to
appear scrunched up.
- Fixed a bug in Make
where
the "inquire motor step" feature would return
the speed for traversing instead of cutting, if inquiring a motor step
on a "slit".
- Abrasivejet feed rate
calculator
now properly uses regional
settings for decimal points in its display of numbers.
- Layout: Possibly fixed
a
bug that could cause a "Invalid Floating Point
Operation" when repeatedly using the True Type Text dialog.
- All applications: Possibly
fixed a bug that could cause the software version to be
reported as "?", which was seen on one computer.
- Possibly fixed a bug that could cause dialog windows to appear
behind the main application windows in Layout
and Make. (The bug
is in Windows XP, and a work-around was added to Layout and Make to
avoid the bug. However, the bug is rare enough that we are not
100% sure it is 100% fixed.)
Rev
9.0
Changes made
since rev "8.0" of the software, which was
released 6/9/2006.
Make
- Fixed a bug that could cause
an
incorrect velocity under just the right set of conditions on
some parts.
This bug could cause the effected portion of the tool path to cut
incorrectly (typically too rough). This bug has been fixed, and
is
the
reason why rev 9.0 has been released so soon after release 8.0. (Any
bug
related to the actual motion of the machine is considered of extreme
importance
and priority.)
Layout
- Added support for additional special characters in Tool Path
Fonts. In particular, it is now possible to create Tool
Path Fonts that support the following new characters: % & $ (
) [ ] { } : ; _ ~ | = ' `. For information on Tool Path Fonts and
how to make them, consult the OMAX Interactive Reference.
- Fixed a bug that could
cause "slits" to not import properly when using the Generation IV DXF /
DWG file import filters.
Rev
8.0
Changes made
since rev "7.0" of the software, which was
released 1/3/2006.
Layout
"Sketch"
tool: You can now sketch using
Splines. Right-click
on the "Circle" button, and choose "Spline (Free-form Curve Drawing)"
(Keyboard equivalent is "%"). Then hold down the mouse while you
sketch on the screen. This will draw a series of short line
segments, similar to the "Continuous Line Draw"
command. When you let go of the mouse button, the entities will
convert to a clean and smooth Spline curve, which is then converted
into a series of lines and arcs, and you can continue to
draw some more. To quit drawing, press the Right mouse button, or
press "Esc", or choose a different command. You can operate this
tool in one of two modes: The default mode is that when
the mouse
button is let up, the "pencil" also is picked up, so that you can
quickly sketch a new curve. The second mode is to always keep the
pencil down, which is useful if you want to specify the curve by a
series of clicks, such as when tracing around an image. When in
this mode, to "pick up the
pencil" press the "Space" bar on the keyboard. This command is
most
useful for artistic purposes, such as hand-tracing images, sketching,
etc., but is not well suited for precision applications.
7 new "Qualities" for doing "Slits":
For each cutting Quality 1,2,3,4,5, "Water-Only" and
"Minimum Taper", there is now a corresponding Quality for
"Slit". These qualities are essentially the same as
Qualities 1-5, "Water-Only", and "Minimum Taper",
except that they will not have any tool offset applied to them.
This means that they cut right down the center-line. On screen, they
are the same color as other qualities, but they show up as dotted
lines. To
access slits, Right-Click on one of the Quality buttons
in the Quality tool bar in Layout, and choose "Slit"
from the pop-up menu. You can also use the keyboard equivalents
of
"Ctrl+1", "Ctrl+2", "Ctrl+3", "Ctrl+4", "Ctrl+5", "Ctrl+8" (Water only
slit), or
"Ctrl+minus" (Minimum Taper Slit).
Improvements
to DXF / DWG filters:
- Added a "Preview" window: This allows previewing the
results of the settings prior to committing to them.
- Specify which "layout" of a drawing to consider for importing,
in the case where a drawing may be composed of multiple views.
- Updated filters to support for yet more "flavors" of DXF and DWG
- Slightly improved error
messages when some kinds of files don't
load properly.
- New Tool Path Font:
"FutureSign",
which is modern looking stencil font. Font courtesy of Bob
Ekstrom.
- Parametric Shape Library
now remembers previously entered settings (if you wish): There
is now a
check-box in the "Parametric Shape Library" dialog that if checked,
will cause Layout to save the entered values for the currently entered
shape, when you press the "OK" button to accept the shape.
Then, next time that parametric shape is used, the edit boxes will
automatically be filled in with the previous values used. (This
feature is also available in Make, since Make also uses the Parametric
Shape Library.)
- File / Open dialog now has an
option for "Open file using Windows style dialog". This is
useful if you need some of the standard features provided by the
WIndows style dialog, such as sorting by date, access to network
drives, etc. Simply right click in the file list of the dialog
for this option.
- Improved "Tab" command:
It is now possible to specify the two legs in the "Tab" command to be
different qualities. Also, there is a new option under the
"Quality" selectors for "Same as part". This is used to set the
tab Quality to be the same as whatever entity you click on. For
example, if you click the tab onto an existing entity that is Quality
of 3, then that piece of the tab specified to be "same as part" will
also be Quality of 3.
- Enter a description for
variables in parametric files: You can now enter an optional
description for each variable in a parametric file. This
description will show up to the user. For example, you can have a
variable named "vRad", and a description of "Outer Radius". The
user will see "Outer Radius". If no description exists, then the
variable name will be used in its place. Descriptions are added
at the very end of the variable declaration line, with a comma
separating it from the other items in the declaration.
- Specify frame length: It
is now possible to specify the line length in the "Frame" command to be
anything that you like. Enter a length of "0" to have the
computer automatically pick a length for you (as it did in previous
versions.)
- When opening an image for
manual
tracing, the "Adjust Image Colors" dialog now automatically
appears. This makes it easy to quickly turn down the
brightness
or make other adjustments, which are useful for insuring that it is
easy to see the CAD lines that are drawn on top of the image.
Note that the "Adjust Image Colors" display may not show up on
exceptionally large images,.
- Automatic Backup now
temporarily disables itself when the drawing size
exceeds 100,000 drawing entities. This is to prevent the
annoyance of a long delay while the backup occurs. It will
automatically re-enable when the drawing size is less than 100,000
entities.
- New Clean Option, "Divide all
entities where an endpoint touches another entity": By
default, this option is turned off. If you turn it on, it will
loop through all the entities in the drawing, and look for spots where
the endpoint of an entity touches the side of another entity. It
will then divide the entity it touches at that location. This feature is most useful if you import
a file from another CAD or CAM program that has leads and traverses
already assigned to it, and you want to make sure the leads
function properly, and cut into the feature they touch.. (So there is
no more need to "I-divide" every lead location one at a time by hand.)
Make
Support for optional Terrain Follower
hardware: There is now an option in the "Advanced /
Administrator Setup" dialog to tell Make that Terrain Follower hardware
is attached to the machine. If this option is turned on, then the
Z-Axis toolbar will contain Terrain Follower options for "On", "Off",
and "Auto". Requires optional Terrain Follower accessory in order
to work.
Automatic dialog closing,
mouse moving, and locking: The "Test Pump" and "Cut off Saw"
dialogs will now
automatically close after 60 seconds of no activity, if they were left
in a condition where an inadvertent mouse press could start the
machine. In addition, the mouse pointer will move away from
buttons that could cause the jet to turn on if pressed, after 10
seconds of no activity. Likewise, the "VCR" style "Path
Controller" dialog will now
automatically move the mouse cursor away from the "Start / Continue"
button, and over to the "Pause" button after 10 seconds. Finally,
in the "Path Controller" dialog, the "Cycles Remaining" edit box will
automatically lock itself after 10 seconds, to prevent accidental
keyboard presses from changing the value. (There is a button to
lock-unlock it manually as well.)
Custom Report Generation: In
addition to the "Print Path" and "Print Statistics" option, there is
now "Print Report". This allows you to print custom reports with
formatting and data of your choosing. You can choose from several
pre-defined templates, or create your own using 3rd party software such
as HTML editors, Microsoft Word or WordPad, Excel, and virtually any
other program that uses ASCII based text files. Reports can
include pictures of the part, logo's, etc., and be as fancy as the
template file that you make. There are over 100 built-in
variables to allow including information from Make (like "Material
Thickness") into your reports. You can also declare your own
variables, so that Make can ask the person generating the report to
provide additional information, such as the name of the company the
report is being prepared for, etc.
Acceleration Smoothing: Starting
with
version 8.0 of the OMAX software, there is a new feature that can
greatly enhance the smoothness and speed of all X, Y motor motions of
your machine. OMAX Calls this feature “Acceleration
Smoothing”:
Benefits
include:
• Run reliably at
significantly higher accelerations
• Eliminate vibrations caused by sudden changes in
acceleration, improving parts that involve high speed motions (thin and
soft materials in particular)
Key
points:
• Version 8.0 of
the software automatically upgrades
you to the new acceleration values
• Acceleration smoothing is turned on by default when
you install version 8.0 of the software.
• The default values are those that work well for all
OMAX machines. However, the advanced user may wish to fine-tune
them to gain extra speed or to even further smooth out motor motions
(For example, increase the acceleration even more, for small machines
such as the 2626 or 2652.)
• The default values are set so that most parts will
take approximately the same amount of time as before.
• For some parts (especially thin parts with lots of
corners), part times may be slightly slower, but the parts will
typically come out significantly better.
• Acceleration smoothing can be disabled by advanced
users.
Technical Description
When the controller asks for a sudden change in the acceleration on the
tool path, the force causing the acceleration must suddenly change.
These sudden changes of force cause vibrations of the machine
structure. In software revisions 7 and earlier these effects were
minimized by simply keeping the accelerations low. Beginning with
revision 8 the permitted acceleration is increased and the rate of
change of acceleration is managed to minimize machine vibration.
There are 3 parameters that an administrator can select to affect the
XY acceleration and vibration of the machine. They are all found on the
advanced setup screens.
As before, the
maximum
acceleration of the machine can be selected.
This value is input in units of g, the acceleration of gravity on the
earth. One g is equivalent to 386.4 inches per second squared (or 9.8
m/s
2.) In software revision 7 and earlier it
was normally set between
.01g and .05g. With revisions after 8, the maximum acceleration should
be set to .15g. There is little reason to adjust it from this value.
The next parameter is the maximum rate of change of acceleration,
maximum
smoothing. It is input in units of inches per second
cubed (or mm/sec
3). The correct technical
name for this parameter (as
odd as it seems) is “Jerk”. The default value of 100 inches/sec
3
(or
2540 mm/sec
3) will give path times shorter
than previous software
revisions in all but the most intricate paths. To shorten the path time
while permitting more vibration, raise the value to 500 inches/sec
3
(or
12700 mm/sec
3). Conversely, to reduce
vibration while increasing path
time, lower the value to 20 inches/sec
3 (or
508 mm/s
3). This parameter
will have the greatest effect on thin parts and traverse lines where
the machine is moving at its highest speeds and accelerations.
The last parameter, max
delta accel, is
concerned with the centrifugal
acceleration perpendicular to the path direction when following curves.
Imagine traveling a straight section and then entering an arc along a
tangent to the arc. On the straight line, there is no acceleration
perpendicular to the travel direction. On the arc, there is a large
acceleration dependent on the speed along the arc. The sideward
acceleration suddenly jumps by an amount dependent on the speed and arc
radius. The maximum permitted value of this jump in acceleration is the
third parameter that can be set, the
max
delta accel.
Choosing a low
value causes the machine to slow at the arc to line joint whereas a
high value permits a high speed with attendant higher level of
vibration. The default value of 10 inches/sec
2
(or 254 mm/sec
2) caused
neither significant slowing nor excess vibration.
The Z axis motion is not affected
by
these settings and is managed as
before by simply specifying a maximum acceleration. The Tx and Ty axes
for the Tilt-A-Jet are only indirectly affected by these settings. In
general, smoother motion of the XY axes will cause smother motion of
the Tilt-A-Jet.
Acceleration Smoothing can be
disabled by setting the values for
maximum smoothing, and max delta accel to one million (1000000).
If acceleration smoothing is disabled, then it is also required to set
the maximum acceleration of the X and Y axes back to the previous lower
value appropriate for your machine (0.01 to 0.05g).
If you have additional questions about this feature, email
techsupport@omax.com
Warning message to home machine: A
warning message regarding the need to home the machine now appears when
Make is run for the first time after a re-boot. (This message can
be disabled in Advanced Setup, if desired.) The purpose of
this
message is to remind the user that it is good practice to re-home the
machine after it has been turned off. The reason it is good
practice, is because when the power is disabled to the motors, it is
possible for the machine to be moved. These movements are not
recorded, which can result in the machine home positions and soft
limits drifting by the amount of the movement. Re-homing
the machine after power-up eliminates this as a possible problem.
Updated to support new "Slit"
Qualities. (See description above for Layout).
- Display pressure in MPa or
Bar,
or KSI/PSI: When the units are configured for metric (mm, cm,
etc.), then there is now a choice to display pressure in units of
either "MPa" (megapascals) or "Bar". This is configured in the
"Configure Display & Units" dialog.
- Parametric Shape Library
now
remembers previously entered settings (if you wish): There is now a
check-box in the "Parametric Shape Library" dialog that if checked,
will cause Make to save the entered values for the currently entered
shape, when you press the "OK" button to accept the shape.
Then, next
time that parametric shape is used, the edit boxes will automatically
be filled in with the previous values used. (This feature is also
available in Layout, since Layout also uses the Parametric Shape
Library.)
- 3D button always shows
up
in make, even if a 2D path is loaded. (Just as a reminder that
this feature exists. Previously, it was invisible except if a 3D
OMX file was loaded.)
- New naming
convention for
temporarily nested files: Instead of saving nests as
"Nest_Temp.ord", the software now chooses a file name that is unique to
the computer the nesting is done with. The file name is now
"Nest_Temp_XXX" where "XXX" is replaced by the machine serial number of
the computer it is on. If the machine serial number is not set,
then it uses the computer's name. This prevents conflicts when
nesting the same file that is stored somewhere on the Network, where
multiple users with multiple OMAX machines might otherwise accidentally
over-write each others temporary nested files.
- BTS files ("Bitstream files)
can
now contain
comments: The A line with "//" in front will be ignored,
allowing advanced users who are hand-editing BTS files to include
comments to make it easier to navigate within the file. (BTS files are
to the OMAX as Atoms are to objects, or assembly language is to
software
- they allow extreme control of the hardware, but are extremely
difficult
to create. For information on BTS files, contact
techsupport@omax.com.)
- Drill piercing small holes
without turning on the jet: If the Drill accessory is turned on,
and there is a pierce point defined by a traverse, then a tiny piece of
"lead", then another traverse (as one would draw for making small
pierces), then the hole will be drilled, but the jet will not turn
on. This works for short "leads" where the lead is shorter than 1
mixing tube diameter.
- Change to Tilt-A-Jet warning:
If the Tilt-A-Jet is enabled, then when previewing a part to the
screen, or when cutting a part, a note will now appear at the bottom of
the preview stating that the previewed nozzle position (or white cross
hair that indicates the nozzle position) may drift slightly from the
original offset tool path, in order to compensate for X,Y motions
introduced by tilting the cutting head. Also, the warning
message with the "Ok" button that appears the first time a preview is
generated is no longer needed, so no longer shows.
- Better support for recording
parts history: If the history file for a part grows to be
larger than about 1.5 Mb, then the older portions of the file will be
removed, in order to keep the file size down. (Previously, the
history would simply stop recording if the file exceeded 1 Mb.)
3D Path Editor
Updated to support new "Slit"
Qualities. (Slits are cutting qualities with no offset.
See description above in the Layout section.)
Updated to support newer video
cards and device drivers with OpenGL 2.0 (previously, an error
would occur when attempting to run the 3D path editor with some device
drivers that ship with OpenGL version 2.0.)
- Added "Draw Path With Arrows"
button
to display the tool path direction in the 2D view.
- It's now possible to "zoom"
in
closer to objects without them disappearing in the 3D view.
- Uses the same "File / Open"
dialog as OMAX Layout. (If you have a need to use the
standard Windows-style file/open dialog, simply right click in the file
list and choose, "Open file using Windows style dialog...")
OMAX Interactive Reference
- Lots of new content has been
added.
- The PDF files supplied with
the
OMAX Interactive Reference are no longer shipped. This is
because we found them to not be very widely used, yet they take
considerable effort to maintain and keep up to date.
Bug
Fixes
- Fixed a bug that could allow the user to use the "go to spot on
path" command while the machine was already running a path.
- Fixed a bug that could cause the machine to be off by one motor
step (0.0005"/.0127mm for most machines, or 0.00025"/0.00635mm for the
2626XP) after the "Go to Spot on Path" command was used.
- Fixed a bug that could cause some DXF and DWG files to not
import
correctly when importing on computers with regional settings configured
with commas to be used as decimal points.
- Fixed a bug that would cause the machine position to be off
slightly after using the "Go to Path Interrupted Home" command on
machines using Error Mapping.
- Fixed a bug where display corruption could occur after using
the
"right-click" option for "Use alternate filters" in the "File / Open"
dialog.
- Fixed a bug where the "Test Pump" and "Path Controller" dialogs
in Make would not appear when the software was installed on an off-line
PC.
- Decreased collision checking tolerance for corner passing, to
prevent a rare conflict where the corner pass might interfere with
another feature of the path, and cause a rough edge, or skipped
cut. (So now, the corner pass will be disabled for that corner.)
- Fixed a bug that would cause parts that are longer than one
dimension of a sheet of material to be nested to, to sometimes nest
outside of the sheet.
- Fixed a bug that could cause an error when loading certain DWG
files.
- Fixed a bug in Make that could cause a part to be cut in "water
only" if a negative abrasive on delay was entered, and "brittle mode"
was turned on.
- Fixed a bug in Make that could cause unnecessary acceleration
and
vibration in some parts
- Fixed a bug that could cause an error when attempting an
impossible fillet in Layout.
- Fixed a bug that could cause a "range check error" when
attempting to load a file with a Quality that is beyond the range of
what the OMAX handles.
- Fixed a bug that would cause the Precision Optical Locator to
activate the automatic squaring of the Tilt-A-Jet, even on machines
that did not have a Tilt-A-Jet installed.
- Fixed a bug that could cause a display optimization to make
shallow arcs appear as lines, and become confusing to users,
particularly when using the "divide" commands.
- Fixed some areas where units would be displayed in all capital
letters.
- Fixed a bug in the "Load Path" dialog that could cause the
"transfer path and drawing" command to fail if the destination path was
exceptionally long.
- Fixed a bug that would cause the left/right justification to be
switched backwards in the True Type
Text dialog.
- Fixed a bug that could cause an improper
offset on the last
cutting element of a tool path, if there was no final rapid traverse
move, and the cutting element right before the end of the path was
broken into
two pieces.
- Fixed a bug that would allow OMAX Intelli-TRACE to (poorly) run
on
systems that do not meet the minimum system requirements. Now if
you attempt to run OMAX Intelli-TRACE on a computer that does not meet
the minimum system requirements, and error message will occur, and the
feature will not be executed.
- Fixed a bug that could cause some arc entities to be "flipped"
the wrong direction when importing some DXF/DWG files
- Fixed a bug that would prevent the "Esc" key from canceling the
"Rotate Copy" command properly
- Fixed a bug that could cause instability of Layout or Make when
files with more than 500,000
entities are open.
- Fixed a bug that could cause the "Enable
Soft Limits" checkbox on
the pull-down menu from properly being checked after checking the
similar check-box in the "Set soft limits by corner and size" dialog.
- Fixed a bug in the Abrasivejet
Feed Rate Calculator, where the "Print Form" option would print
without showing the text in the comboboxes.
Other:
- The "Esc" key can now
be
used as a shortcut for "clear" in the OMAX
Calculator.
- OMAX Tester now shows
bit
for "Follow Z1" and "Follow Z2", which are used by the terrain follower
accessory.
- Technical Support Reports
now contain additional information:
- Which video display devices are available (video card
information)
- Screen-capture of the screen when the last exception error
occurred
- Whether or not Windows Vista is running
- Location of the Windows "Temp" directory.
- The bitstream image of the tool path (individual calculated
motor movements) will now be included in the report if it's less than
150Mb (previously, it would not be included if greater than 50Mb)
Rev
7.0
Changes made
since rev "6.0" of the software, which was
released 10/26/2005.
Layout
Intelli-TRACEtm Automatic Raster
To
Vector conversion: The Image Tracing features has been greatly
expanded to support an
automatic mode for automatically tracing raster based images along
areas of high contrast, and converting the raster image into a vector
image suitable for editing in Layout and eventually making into a tool
path. To access this feature, use the "Image Tracing" pull-down
menu at the top of Layout. Manual tracing is also still available.
Image Tracing (Manual and Intelli-TRACE)
now supports a wide variety of raster
file formats. The following file filters
are
now supported: *.tif; *.jpg; *.gif;
*.bmp; *.ico; *.png; *.cur; *.jp2; *.pxm; *.j2k; *.emf; *.wbmp; *.wmf;
*.avi; *.wmv; *.mpg; *.crw; *.dcx; *.tga. Note that only
the very first frame of video file formats (*.wmv;
*.avi; *.mpg) is loaded for tracing, and that full support for these
file formats may depend on installed CODECs. For animated gif
files, or
tiff files with multiple images, it is possible to specify which frame
to trace by clicking on it in the preview window of the Open Picture
dialog.
- Change the default pixels per
inch property used in Image Tracing to 96 pixels per inch
(typical screen density for a computer screen). Previously, it
was 300 pixels per inch.
- Faster bitmaps: Zooming
raster images works a little better now (faster), as well as is a bit
more
reliable when running on computers with buggy or conflicting video
drivers.
- New tool path font: Ariel
Diamond: This is a variation of the Ariel font. When it is
typed in, it creates a connected font within a diamond grid. This
(and many other) fonts are courtesy of Bob Ekstrom of Zimmerman
McDonald
.
For information on making your own custom Tool Path Fonts, consult the
OMAX Interactive Reference and / or training
videos . OMAX will pay money for high quality tool path
fonts. Contact techsupport@omax.com for details.
- It is now possible to type
in
spaces all by themselves (with no
letters) when entering in text in the Tool Path Text Dialog. This
allows making geometry from just the "space" character (for example,
making a diamond grid using the space character in the new "Ariel
Diamond" font.)
Make
- If the Tilt-A-Jet is not square prior to opening the Precision
Optical Locator "Locate" form in Make, then it will square
itself. This prevents mistakes of using the POL when the
Tilt-A-Jet is not square.
- It is now possible to specify "HomeStepsFromHardStopX" and
"HomeStepsFromHardStopY" In the MakePreferences.INI file to specify how
far from hard stops the actual "Absolute Home" should be located.
This is used by OMAX when creating error maps for the OMAX
2626 xp machine.
Bug Fixes
- Fixed a bug in Layout's Rotate-Copy command where if an XY
value
was specified, and the local zero was not at the same position as
absolute zero, then the rotation point would be in the incorrect spot.
- Fixed a bug that would cause the very last line of a .OMX file
to be ignored
- Fixed a bug that could cause an application error when
importing
some 3D DXF / DWG files
- Fixed a bug in the Precision Optical Locator calibration dialog
that could cause the calibration values to be lost when units other
than Inches are used.
- Fixed a bug in the expression evaluator that could cause the
expression to be incorrectly evaluated when evaluating trig functions
that result in negative numbers. This applies to anywhere where
numbers are entered in as mathematical expressions, but is most noticed
in the OMAX Calculator, Parametric Shape definitions, and the "Function
Plot" feature of Layout..
Other:
|
- A new utility "OMAX Error Map Maker" has been added to the
installation. This utility is not for general use, but is used by
OMAX Technicians for the purpose of making error maps. (Error mapping
is a method for significantly
increasing the positioning accuracy
of the machine. This is useful for the highest precision applications -
especially where high precision must be maintained over large
distances. Error mapping is standard on the OMAX "xp" machines, but can be applied to
any OMAX. Contact OMAX for information on having error mapping
performed on your machine.)
Rev
6.0
Changes made
since rev "5.0" of the software, which was
released 4/18/2005.